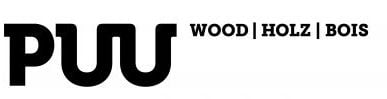
Arola Apartments – As Oy Kirsikka in wood and As Oy Kide in concrete
The Arola Apartments project includes two four-storey apartment buildings built in Hirvensalo, Turku: one wooden and one concrete. Funded by the Housing Finance and Development Centre of Finland (ARA), the project aims to study the effect of different building materials on construction speed and on the carbon footprints and handprints stemming from construction and occupancy, as well as the comparative life cycle costs and the satisfaction and community spirit of residents.
Read the article in Finnish: Arolan kerrostalot
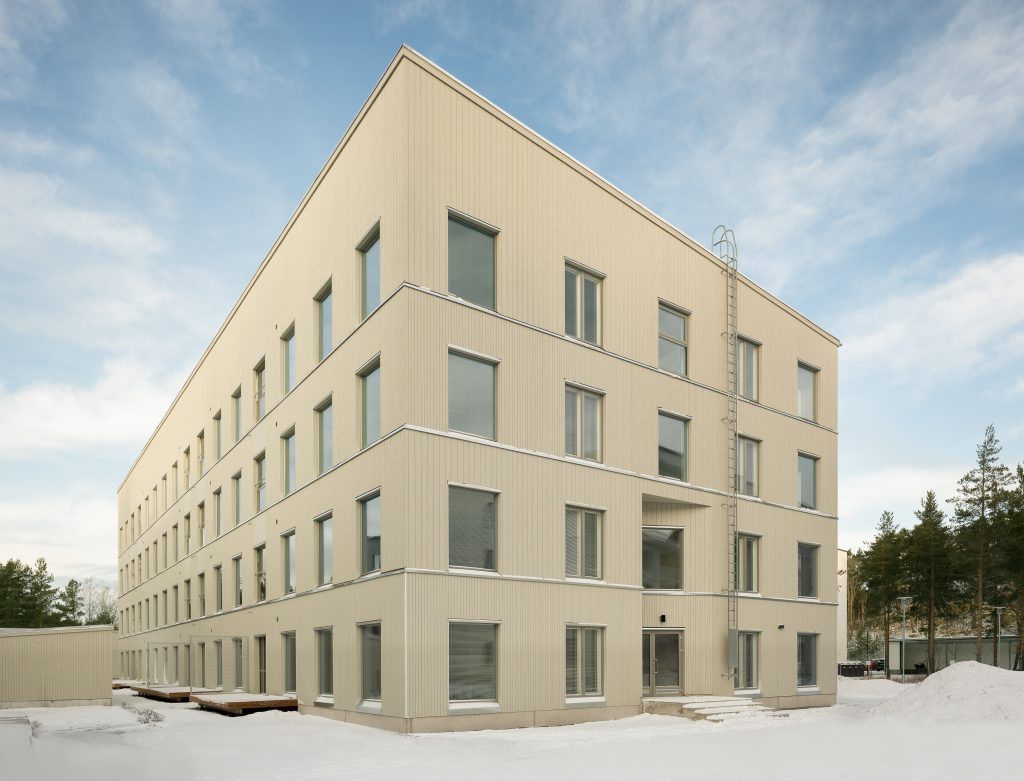
The site sits amidst the natural beauty of Turku’s Hirvensalo, a newly built up area surrounded by the sea. The existing building stock of replicated apartment buildings is being rapidly filled in with new construction, adding diversity and providing the Turku region with another pleasant residential option.
Located on the same plot, the buildings share a common courtyard that has a communal building with saunas and storage for outdoor equipment. Parking on the site is partially covered, with personal storage spaces for some of the residents placed next to the carports. The yard between the buildings brings residents together, with the sauna and club rooms of the communal building offering activities.
At its core, the comparison project sought to design two absolutely identical buildings that differ only in their building materials. The target was to keep the room dimensions and ceiling heights in the apartments exactly the same despite the different structural dimensions. Namely, the wooden building is slightly longer, thicker, and higher than the concrete because of its greater structural thickness.
This meant more time than usual on the design table for both buildings as they needed their own detailing designs and harmonisation.
The building masses and openings are restrained and classic to give the materials center stage. The building frames and facades are both made from either wood or concrete, depending on the building. Large CLT elements were selected for the wooden building, while reinforced concrete elements were used for constructing the concrete building. The facades of the wooden building use light, painted vertical panels that appear to vary in width from one storey to the next. The variation is actually achieved with decorative grooves on the cladding panels used on every other floor. The outer shell of the concrete building is made from natural-coloured, grooved concrete, with the width of the grooves again varying from one storey to another. Galvanised, sheet-metal horizontal strips were added between the storeys of the wooden building to facilitate the installation of firebreaks and cladding. While they serve a practical purpose, these seams also visually divide the building into harmonious parts. Horizontal seams were also added to the facade of the concrete building to keep the chitecture unified, even though there was no need for them for fire safety or other structural reasons.
There was also a focus on community inside the building. The stairwell runs through the entire building mass and provides a street-like space where residents can meet. The stairs zig zag from one storey to another, which encourages residents to take different routes and have random encounters with each other while offering more ways to get around.
There are 82 apartments in total, 41 in each building. The apartments are compact, but comfortable, and vary from 35 m2 studios to large family apartments. However, most are one bedroom units, ranging in size from 51 m2 to 55 m2. All apartments have a retracted balcony, and ground floor apartments have a terrace. The material world of the building exteriors has been extended to the interiors: the interior walls in the wooden buildings have exposed CLT surfaces, and the concrete building has unfinished, natural-coloured concrete inner surfaces.
Technical solutions
Structures in the Kirsikka wooden building are wood to the extent possible. Large CLT elements were used for the exterior walls and the partitions between apartments and stairwells, while Kerto-Ripa slabs were used for intermediate floors. The roof structure is CLT slab with a nail plate truss. CLT was used to make balcony slabs and stair frames, while glulam was chosen for the columns and beams for the retracted balconies. Only the structures, foundations and subfloor of the civil defence shelter are concrete. Stiffening is mostly achieved with massive CLT wooden walls.
All the building utilities were placed outside the apartments, in conduits running in the stairwell. This kept the fire safety and sound insulation solutions functional and simple, and made maintenance easy since no access to the apartments is needed.
The building is fire class P2, and has sprinklers throughout the structure. Fire compartments were created according to usage type: the apartments, exits, technical facilities, and shared storage spaces each have their own compartment. The communal stairwell solution at the site is unusual as it cuts through the entire building. Because the stairwell length exceeds what the regulations allow (more than 24 m), three 1m2 smoke extraction hatches were added to the stairwell and its sprinkler system was enhanced.
Surface class regulations defined what surface materials could be used in the stairwell, which means the CLT stairs have no visible wood surfaces among other things. In accordance with the regulations, the total unclad area of the outward facing walls in apartments is a maximum of 20% of the total surface area of the load-bearing, partitioning, exterior walls, and roof. The facade cladding on the ground floor is treated with fire retardant, as are the balcony interiors and the upper and lower sides of the emergency exits.
The acoustic design was done in accordance with the relevant ordinances and regulations, and there were no separate acoustic requirements for the building itself.
Construction project
Draft designs began in May 2019, with the building permit submitted in November of the same year. Construction started on both buildings in July 2020. The site was finished in January 2022, with the wooden building being already completed 1.5 months before the concrete. All work was under a turnkey contract.
The wooden frame started to go up in October 2020 and was complete in March 2021. Weather protection proved extremely useful for the project because of the winter’s extensive snow. When the installers put up the wooden elements, they had to pay special attention to the dimensional accuracy of the ground floor. In general, the tolerances were finer than for the concrete building. On the other hand, the storeys above the ground floor were easier to install precisely because of the dimensional accuracy of the elements.
It was significantly easier to lift and attach the wooden elements than to work with the concrete building as the lower dry weight of the CLT elements made them much lighter. Since significantly more wooden elements could be delivered in a single delivery, the wooden building also needed far fewer deliveries. The individual wooden elements are also larger than concrete ones, which meant less installation was required.
In wood construction, element surfaces are far from finished when they arrive from the factory, leaving a lot of work to be done on site. The aim is to improve prefabrication finishing for future projects.
Comparison of the wooden and concrete buildings: carbon footprints and handprints, construction costs and timelines
THIS PROJECT has produced information on the relative carbon footprints and handprints, construction costs, and construction times of the two building types. Differences in the carbon footprints and handprints stemmed mostly from the different building materials. The wooden building has the far better carbon handprint of the two because the CLT frame stores carbon throughout its life cycle. The carbon footprints are fairly similar as the annual emissions from the two buildings are mostly the same. The wooden apartment building’s carbon footprint is 11.70 kg CO₂ₑ/m₂/a, while the concrete version is a somewhat higher 12.89 kg CO₂ₑ/m₂/a.
When it comes to the carbon handprint, specifically benefits in annual emissions, the wooden building is the clear winner. Its carbon handprint is -8.13 kg CO₂ₑ/m₂/a, while the concrete weighs in at -1.88 kg CO₂ₑ/m₂/a. Calculated over the entire 50 year building life cycle, the wooden building has total emissions of 1,764 t CO₂ₑ and the concrete 1,917 t CO₂ₑ.
Both buildings use district heating as their heat source, and energy consumption during use is the largest source of emissions in both buildings.
In terms of the total construction costs, the wooden building proved to be about 10-15% more expensive than its concrete counterpart. The price difference comes from design time, materials, and on-site work.
There are only a few people who are skilled at designing wood construction, which means more time needs to be spent on planning and oversight. Design methods for wooden apartment buildings are also not as clear as those for concrete construction. Acoustic and fire safety solutions require special attention, which means their design and detailing may take more time.
Wood is more expensive than concrete as a material, particularly CLT, which contains a lot of wood. There are also fewer CLT suppliers in Finland than concrete, which means there is less competition for tenders.
The required weather protection and the on-site work to finish construction components increase costs. Weather protection can reach up to 5-10% of the construction costs. On the other hand, weather protection has its benefits: work can be done in dry conditions in several shifts, which speeds up the process. Interior work can also start immediately once the frame is in place because no one needs to wait out drying time unlike with concrete. This means weather protection also reduces winter construction costs.
The intermediate floors and partitions in particular are expensive because of how much work still needs to be done on site. The prefabrication of these components is quite basic, and it takes a lot of work to finish them. The acoustic and fire safety requirements also require a lot of attention.
Construction on both buildings began at the same time in July 2020, but the wooden one was completed 1.5 months before the concrete in early 2022. Installation of the elements and the interior work were done simultaneously thanks to the weather protection. This was a clear advantage over concrete construction. However, the unfinished nature of the wooden components slowed things down. Finishing the components required many hours of hands-on work.
Potential residents found the wooden and the concrete buildings equally appealing and had no preference in advance. TVT will conduct the first survey of the residents later this year. This survey will provide more detailed information on the experiences of the residents on the visibility of the materials, the acoustics, the light, the temperature, and the community spirit. Thus far, the residents have been generally satisfied with their new homes.
CREDITS
Lundén Architecture Company is a Helsinki-based office focused on the development and innovation of the built environment, architecture and urbanism. Founded in 2008, the office’s unique approach is shaped by the experiences of over 300 projects to date. The LAC organization is structured as a cluster of studios, each with their individual focus and area of expertise. With a rich palette of knowledge and skills, the studios support and inspire each other to develop and excel in their work. At Lundén Architecture Company, the internationally diverse team shares one vision – to produce innovative and sustainable solutions.
Anu Tahvanainen is an experienced architect specialized in housing and wooden construction. She works in a studio that is focused on multiple scales of sustainable architecture and urban design and new ways of thinking participatory design methods.
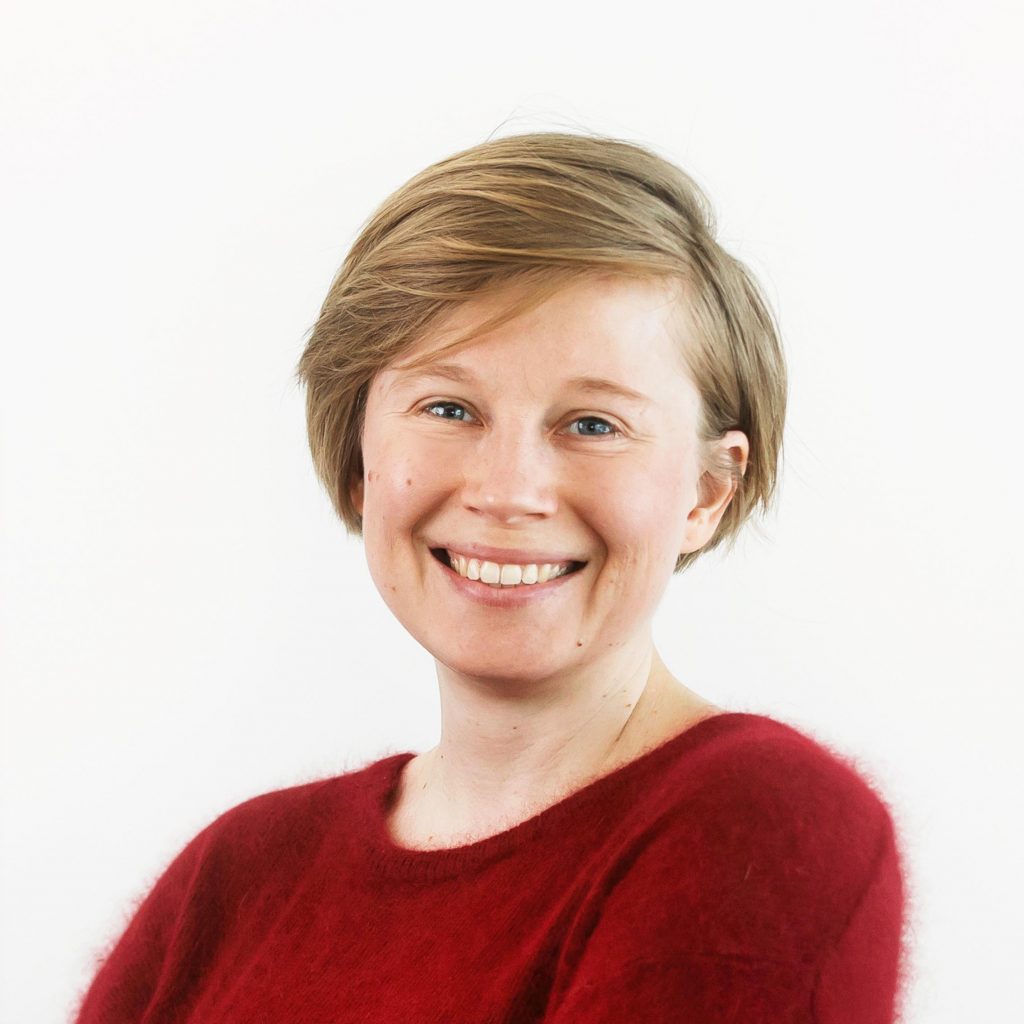
Project in brief
AS OY KIRSIKKA
- Location | Turku
- Purpose | Apartment building
- Constructor/Client | TVT Asunnot Oy
- Year of completion | 2022
- Floor area | 2 612 m2
- Volume | 10 430 m3
- Investment costs | €15.4 million for the entire project (two buildings, wooden and concrete)
- Architectural Design | Lundén Architecture Oy, Anu Tahvanainen, Emma Koivuranta, Eero Junkkari, Bertta Röning
- Structural design | Sweco Rakennetekniikka Oy
- Acoustic design | Akukon Oy
- Fire safety design | LK-Paloinsinöörit
- HVAC design | Insinööritoimisto Petri Vuorela Oy
- Electrical design | LP Electric Oy
- Main contractor | Mangrove Oy
- Wood component supplier | Timberpoint Oy
- Photographs | Wellu Hämäläinen
- Text | Anu Tahvanainen