TOAS Lumipuu
Built for the Tampere Student Housing Foundation (TOAS), the site has two 6-storey apartment buildings made from CLT volumetric elements. The project is the result of a student architectural competition.
Read the article in Finnish: TOAS Lumipuu
An idea competition for wood construction-based student housing was organised at Finnish schools of architecture at the end of 2019 and served as the basis of this project. Architecture students Aleksi Kraama and Eero Kuokkanen created Tampere’s winning submission, Lumipuu, which has now been brought to life.
The proposal drew on forest themes, natural forms, light, and views, and was designed to fit into the surrounding, now almost completed block. During the design phase, the question was how to sculpt a concept that was repeatable, functional and unique with an interesting urban vibe – that would also meet the requirements of the municipal zoning plan, use volumetric elements in the construction, and be popular with residents.
The resulting complex is based on a side corridor and mirrored masses. The stairwell has abundant light, the balconies provide a feeling of the outdoors, and there are comfortable communal spaces. The styling focuses on the vertical nature and lightness of the building mass. General themes of the proposition include the pleasant atmosphere of wooden architecture, modularity, environmental-friendliness, flexibility, spaciousness and communal spirit.
Both buildings balance symmetry and asymmetry under their gabled-roofs. The warm wood tones of the balcony areas enliven the white facades. The building mass is a balance of tower-like areas and lighter sections. The large facade themes and the way the buildings mirror each other hide the modular nature of their construction. The modular apartment floor plans are a good match for the building mass and its side corridor stairwell solution.
Although the common spaces have been significantly reduced from the original submission, the completed building still retains a balance of communal life and privacy as set forth in the competition guidelines. Despite pressures to be efficient, the natural light of the stairwells, the views, and the straight staircase of the original proposal were preserved.
The balconies, on the other hand, were subject to strong cost pressures. In the completed design, the cantilevered balconies are of standard width but very modest depth.
When designing the cladding, sheeting and other facade details, the junctions of the volumetric elements received special attention. From a design perspective, the cladding had the challenge of being pre-attached to the elements for the most part. Balcony detailing was also given plenty of thought. Contrasting facade surfaces and the sheet metal details connecting them frame and emphasise the entire building’s shape. The combination of the cool white paint and the luxurious glazing highlights the facade’s openings and the lines of the building mass. Both facades have their own opening patterns.
Within the limits of fire safety regulations, the aim was to keep wood visible in the building interiors. It was even possible to leave CLT element frames in sight in some of the ceilings, and the door and window details and mouldings also add a touch of wood to the interiors. The CLT is also visible in the staircase elements in the stairwells.
Technical solutions
The buildings are fire class P2 and come equipped with automatic fire extinguisher equipment. The ground floor facades were treated to surface class B. The balconies serve as emergency exits and are equipped with sprinklers. From the first floor upwards, the wooden cladding on the facades only needed to be class D thanks to the firebreaks between storeys. The balcony roofs have been treated to class B. It was possible to leave 20% of the ceiling or wall surface visible in interior spaces in each fire section. This allocation was used to leave the CLT frame visible in living room ceilings.
The acoustic design was a special challenge as a tram line ran by the front of the site, something that was not there during the design phase. The end stop of one of Tampere’s new trams is less than a block away. The connection between the concrete foundation and the CLT modules was leveraged to isolate the building from the vibration. In building B, the foundations needed no separate isolation as the concrete ground floor connection to the modules on top of it was used instead.
The interconnections between modules and the various options for stiffening the buildings against wind stresses were carefully studied during the structural and element design phases, resulting in the development of usable solutions. To calculate potential total stiffness, the studies included empirical testing of how well the vibration isolation components could transfer loads between modules. The architectural, volumetric element, and structural planning all came together to determine the appropriate placement of the steel plates and screws binding the modules together, taking into account work site safety and efficiency and the final finishing of the cladding.
Air conditioning equipment was placed in the attics, and the shared heat distribution room is located in the concrete ground floor of building B. Both buildings have solar panels that allow them to attain energy class A. The technical access conduits are mostly located in the shafts opposite the stairwell of the element modules.
Construction project
Project design began on December 30, 2019. This was the submission date of an architectural competition organised for students. Aleksi Kraama and Eero Kuokkanen, students at the time, won the competition and then teamed up with Arkkitehdit LSV Oy to plan the actual construction. They held their first planning meeting in March 2020. Aleksi Kraama served as project designer for LSV until work at the site was completed.
The element contractor was actively involved in the design phase and was a member of the team from the very beginning. There were a few rounds of restructuring and pruning during the planning phase to bring the project’s costs down to a reasonable level. The most noticeable adjustment was to the floor plan, significantly increasing the floor area and the number of apartments. The buildings went from 76 apartments to 120 apartments, for a net increase of about 1300 asm². Of course, this change impacted the dynamics and volume of the building mass. From the viewpoint of the prevailing conditions and construction costs, the optimal location for the civil defence shelter was determined to be the ground floor of building B. When it came to the exterior cladding, the approach shifted from building it on site to using pre-installed components. This added its own challenges to the facade’s detailing design. The balconies were also cut back during the pruning phase, and the sauna facilities were transferred from the attic to the street level. The planned commercial space was also completely abandoned.
The main contractor was hired at the end of 2021, which allowed the project’s design work to benefit from their experience in cost control. Events across the world, including the Covid pandemic, the Russian invasion of Ukraine, and fluctuations in construction material prices, naturally impacted the project schedule and construction phase. Including contractors in the design phase meant changes could be made early. This kept the project within its cost guidelines despite the extra design work.
Element delivery had its own separate contract, and everything else was under the main contract. Construction began at the beginning of April 2021 with element installation following in early September 2021.
CREDITS
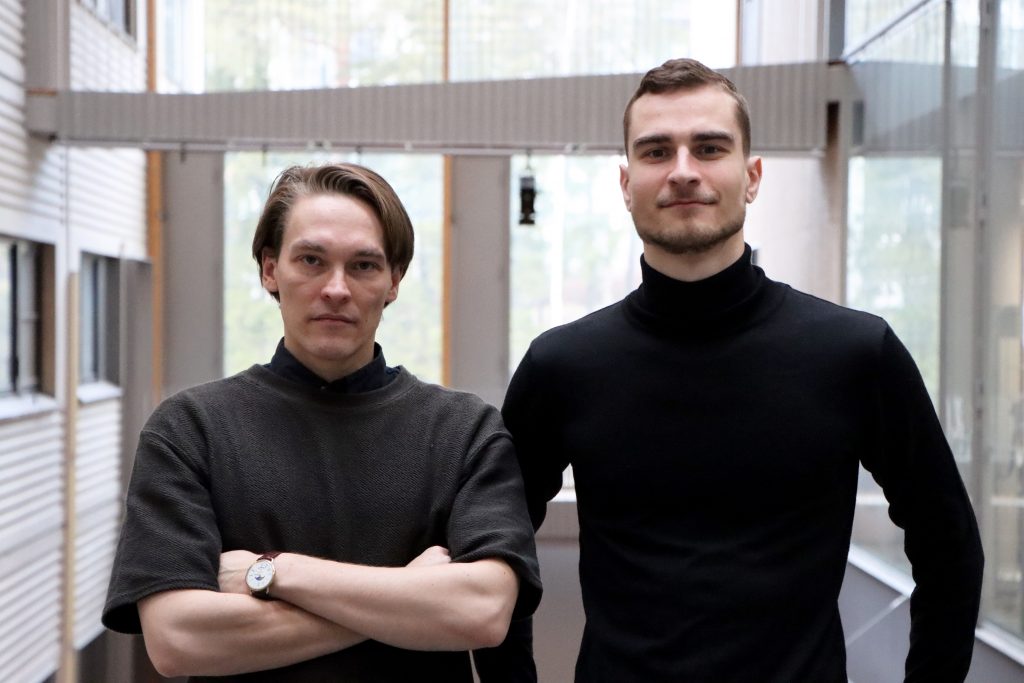
The Lumipuu project has its own thesis: Student apartment buildings with CLT volumetric element construction from idea to implementation – research-by-design, Kraama, Aleksi (2021).
Project in brief
TOAS Lumipuu
- Location | Hervantajärvi, Tampere
- Purpose | Residential apartment building
- Year of completion | 2022
- Floor area | 5 403 m2
- Total area | 6 204 m2
- Volume | 19 983 m3
- Investment costs | 14 150 628 €
- Architectural Design | Arkkitehdit LSV Oy
- Structural design | A-Insinöörit Suunnittelu Oy
- Acoustic design | A-Insinöörit Suunnittelu Oy
- Fire safety design | L2 Paloturvallisuus Oy
- HVAC design | Granlund Pohjanmaa Oy
- Electrical design | Granlund Pohjanmaa Oy
- Main contractor | Rakennusliike Tikirak Oy
- Wood component supplier | Elementti Sampo Oy (volumetric elements), Oy CrossLam Kuhmo Ltd. (CLT manufacturer)
- Photographs | Roope Jakonen & Mika Huisman
- Text | Janne Laukka