TOAS Kauppi – beautiful and sustainable for students

Located along the new Tampere tram route, TOAS Kauppi offers apartments near outdoor, sports, and educational venues. Made with CLT volumetric elements, Kauppi is the first wooden apartment building built by TOAS, the Tampere Student Housing Foundation.
Text: Ida Väänänen | Photographs: Skyfox, Marko Kallio
Read the article in Finnish: TOAS Kauppi – kaunista ja kestävää opiskelijoille
TOAS Kauppi is part of a complex that borders the TAYS (Tampere University Hospital) hospital, an allotment garden, and the Kauppi sports park and outdoor areas. Five different types of residential buildings and an above-ground parking garage are located around a shared courtyard. Bst-Arkkitehdit Oy was responsible for the principle and construction design of four residential buildings, the parking garage, and the courtyard. The overall idea of the architecture was to have the building exteriors accentuate the different housing solutions. As a result, the buildings have facades made from different materials, including hand-made brick, sanded plaster, and metal mesh. With its wooden surfaces, TOAS Kauppi complements the material selections of the rest of the complex. The starting point of the architecture was to design and build a building that meet the needs of the developer and fits into the cityscape in a beautiful and sustainable way. Architect Ida Väänänen from Bst-Arkkitehdit was the principle and construction designer for TOAS Kauppi.
The untreated planed larch selected for the facade cladding emphasises the component-like nature of the building, and the calming repetition of the window composition adds texture. The straight horizontal cladding blends out the horizontal seams of the facade’s CLT elements. As a deviation from traditional wooden construction, the vertical seams have novel detailing and the corner boards were replaced with metal cap mouldings. The exterior architecture follows a few select themes, which is more than enough at this location. The folded facade shape provides residents with views into different directions and gives the building a distinctive recognisable character. The roof, which slants down in one direction, conceals the air conditioning equipment room. The wooden storeys are built as extensions on top of the concrete foundation, which was easy to do with CLT module technology.
The choice of surface materials for the interiors was influenced by the fire and acoustic requirements and long-term durability. However, there was a desire to leave as much wood exposed as possible. In the apartments, the CLT roof surfaces were treated with a translucent fire retardant. Clear varnish was used to treat the interior frames of the wood-aluminium windows and French balconies. The wood surfaces of the CLT apartment module support consoles, CLT elevator shafts, and the undersides of the stairs were left exposed in the corridors and stairwells. These surfaces were treated with wood preservatives.
TOAS KAUPPI HAS 8 FLOORS. The ground floor, built from concrete, contains a bicycle storage room with bicycle maintenance facilities, storage facilities, a civil defence shelter, communal sauna facilities, a club room, and a laundry room. Floors 1 to 7 are built from wood, and house a total of 70 student apartments.
The building’s fire class is P0(2). The basis for the fire class P0 assessment is the deviation from the exit requirements and a comparative functional risk assessment of the building prepared by the fire designer. The basement, floors, and attic are separate compartments (not including the stairwell), and these compartments are further split up by purpose as required. The building has one fire-protected exit, and the entire building has an automatic fire extinguishing system. The exit arrangements for the building are not officially based on emergency exits, so there are no requirements for the French balconies in the facade.
The spread of fire between overlapping windows and other openings is suppressed with automatic fire extinguishing equipment. In the facade’s ventilation gap, the spread of fire is suppressed with fire dampers on each floor. Smoke removal relies on gravity and takes place mainly by fire department measures through windows and doors. The smoke removal from the stairwell is through the smoke removal hatch located at the top of the stairs.
The site’s acoustic design had to account for the helicopter traffic noise in the adjacent TAYS hospital area. Some of the outer walls were clad on the inside with triple gypsum board to ensure the outer casing met sound level difference requirements. In addition, the acoustic properties of various doors and windows weighed in heavily in their selection from an early stage.
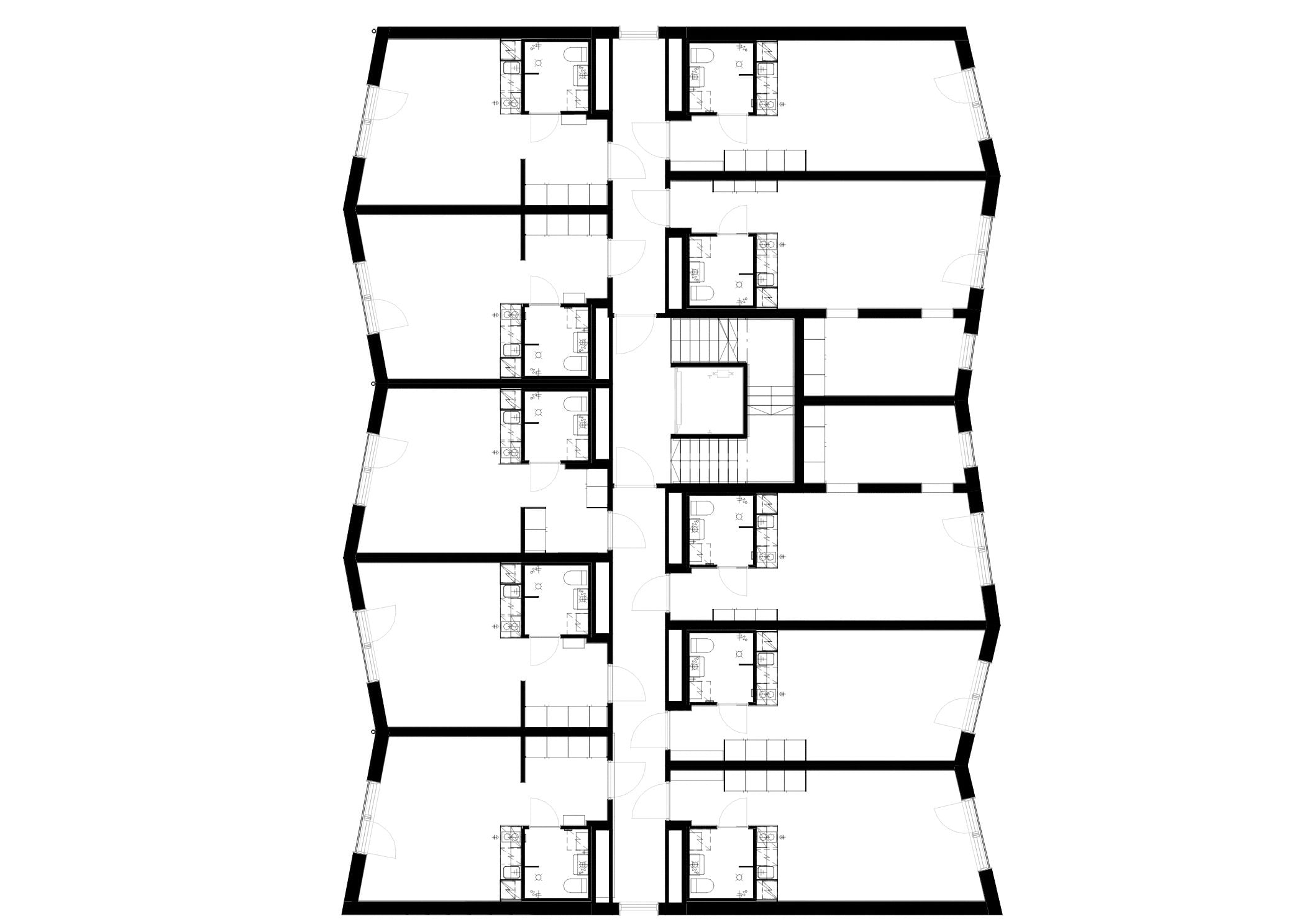
THE DEVELOPER KICKED OFF the planning for the site in November 2019 with project design workshops where different solution models “sparred” in a multidisciplinary exploration. From the beginning, the goal was to combine superior wood architecture and functional technical solutions. Maintenance played a key role in the decisions, while the cost implications of the different alternatives were also carefully investigated. Having the principle designer involved in evaluating and brainstorming solutions already from the project planning phase was significant. Many ideas from the initial stage were then further refined and polished during the project design phase. Some ideas will be saved for other projects. The collaboration between the designers, the developer, the main contractor and the component supplier was constructive and forward-looking. The entire project team also sought to work towards common goals during the construction phase. Work started on site in June 2020. Installation of the CLT volumetric elements began in November 2020, with the site being handed over in May 2021.
The article has been published in October 2021 in Wood magazine 2/2021.
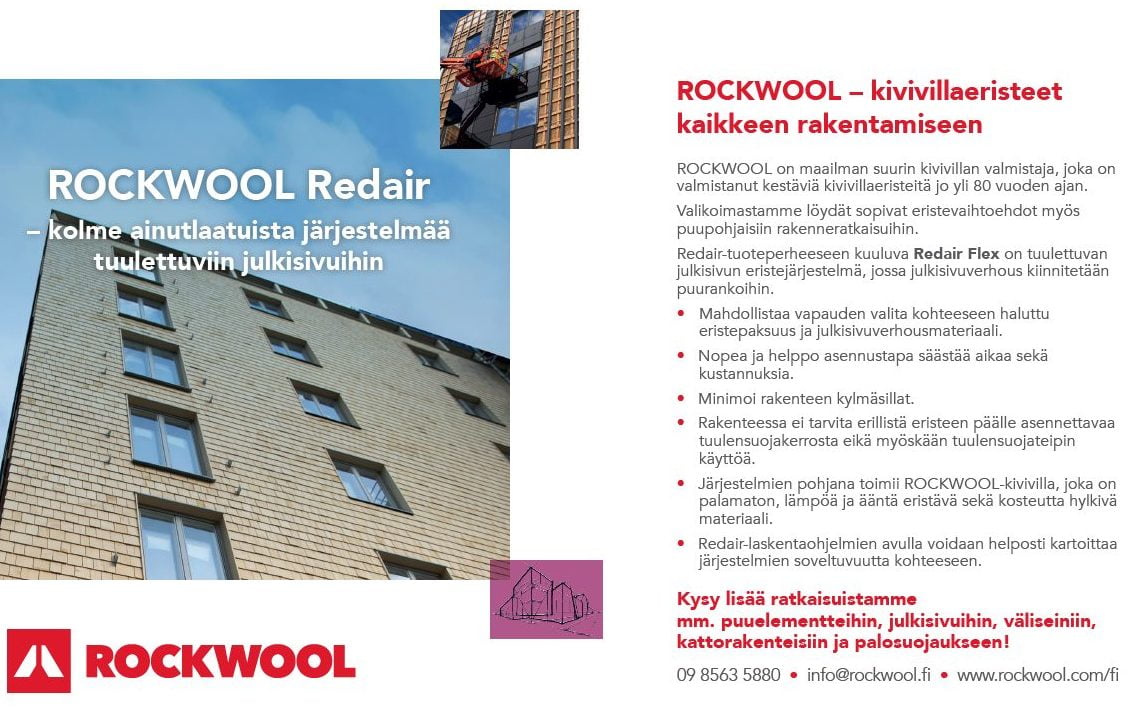
- Read the whole Wood magazine 2/2021.
- The next magazine will be published in the spring of 2022. Subscribe it now.
- Articles selected by Wood Magazine advertisers are published as e-articles in addition to the print magazine.