The ABCs of houses
Coined by the folks who worked there, the term “top of the tops” describes our construction site, with Kurttila’s old buildings, the nearby idyllic Kauklahti, and its own scenic nature giving the area a special appeal. The name “Aakkostalot”, ABCs of houses (houses A, B, and C), is derived from the address, which reflects the important, historic role Kurttila played as an educational centre in Espoo. The buildings are nestled down amongst a green pine grove high on a rock face.
Lue artikkeli suomeksi täältä.
A joint management agreement covers the plot, which is split into three sections of slightly different sizes designed to give each unit an individual feel. Parking is hidden between the houses, with direct entry from the carports to the residences. The building masses follow the flow of the terrain, making the quarried and smooth rock a natural part of the gardens. The living rooms in houses A and B are on the sunny first floor, opening on extensive views out east to Kauklahti and west towards the setting sun. In house C, the main living space is on the ground floor. Every house has an open stairwell connecting its floors, and the balconies and canopies expand the interiors into the adjacent gardens.
The nature of the site set the design parameters for the type, number, and size of the buildings, as well as the number of floors and room layout. Although it may have led to more work, we decided to build three different buildings of slightly different sizes and with different yards. This allowed us to take maximum advantage of the flow of the rocky terrain, the surrounding vegetation, and the long unobstructed views. The municipal zoning plan protects the site’s pre-existing pine grove.
Since there was no external client, we were able to follow an architectural vision of timeless and environmentally friendly material choices without having to chase the design fads of the day. The selected project model gave us a more liberal timeline, which meant the project could include aspects that would be impossible on a tighter schedule. Examples include items such as polished concrete floors on the lower storeys, visible use of wood in the interior spaces, pine panel and birch plywood interior cladding built on site, and all-wood laundry room furniture and interior stairs. The deliberate pace of the construction meant structures had enough time to dry and new materials could air out, resulting in healthier living conditions for everyone. Built in an increasingly urban space, we chose three different shades of green for the building exteriors to help them blend into the former park’s surroundings. This also provided an affordable way to stand out from the monotony of black-white-grey new houses.
In a project like this where the schedule is not packed and decisions can be made off-the-cuff, any necessary changes and development ideas that arise during construction can be added without turning the project upside down.
The extended schedule had the additional benefit of leaving the gardens time to grow, giving the completed buildings an edge on the market with their finished landscaping. The buildings were not fully furnished at the time of sale, and buyers appreciated this opportunity to select some of their own fixtures and furnishings as well as certain structures used for defining layouts.
This deliberate pace, which could also be conceptualised as “slow design”, includes environmentally friendly thinking. When architects are financially responsible for the long-term result, they are more likely to commit to balanced and sustainable solutions for the building and roof shape, energy efficiency, and surface treatments etc.
Technical solutions
The buildings have pole frames, intermediate floors with Posi-lock bars, and lattice-work roofs. The building frames are stiffened with Visa roofing and gypsum board on the ceiling of the top floor. The intermediate floor level is stiffened with 18 mm thick OSB panels that transfer the horizontal shear to the upper part of the outer walls and the load-bearing and stiffening partitions. The exterior walls are stiffened with 9 mm thick gypsum boards that transfer the loads onto the foundation. Gypsum boards on the stiffening/load-bearing partitions provide additional stiffening.
The larger houses B and C have modular indoor air heat pumps integrated with the air conditioning, heating, and hot water heating. Building A is the smallest and uses an exhaust heat pump for ventilation and heating. Both heat pump solutions have an energy class rating of A+, and all the residential units have underfloor heating using circulating water.
The electrical wiring in all houses follows a variable star-like installation. All interior and exterior spaces use LED lighting, mostly with LED light strips in the suspended ceilings. The living room and kitchen ceilings have a 3-phase light track, while the yards have pole lights and the driveways have bollard lights. The carports have recessed lights equipped with motion sensors, whereas the other outdoor fixtures have standard adjustable outdoor lights. The fire alarms are connected to the electrical network, and there is an option for a 3-phase charging port for an electric car.
EI30 gypsum board, which covers the canopies and the exterior walls all the way up to the roof, separates the residences from the garages and carports.
The construction project
The site was acquired in autumn 2017, with the planning and construction permit following in spring 2018, and the excavation, earthworks and foundation work starting in summer and autumn 2018. The building frames went up at the beginning of 2019, with houses A and B being inspected and sold in 2020. House C had its interior work completed in 2021 and was sold in spring 2022.
Constructed from non-insulated frame elements, the building frames of all three houses went up side by side, as did most of the interior structures. The finishing work was done in stages. To support the goal of avoiding plastic, fibre insulation was used for the thermal insulation in the wooden structures. The element supplier was able to customise the window openings and the details on the exterior cladding, eaves and openings as requested. The construction and building technology work was mostly contracted for an hourly wage with two contractors on site, each for one year. On site, Markku Sonninen handled the design of the details as the work progressed and was in charge of the management and procurement of materials and municipal utilities. He also handled most of the visible interior and panelling work, including the interior stairs, the bathroom counters and storage fixtures, and the birch plywood cladding. Satu Ratinen oversaw the financing, general supervision and cleaning of the work site, the design and construction of the yards, the installation of the terrace planks, and the protective treatments for the bathrooms. The architects found the inter-mixture of roles to be a good learning experience. They also handled the sales themselves, selling the houses immediately once finished.
Looking back, the architects feel that this blending of management roles improved both the process and the end result. When you track and fill in the cost calculation sheet for a construction site yourself, you have a much better idea of the actual costs, leaving you with a better understanding of what “real developers” go through. Working side-by-side with construction and installation workers and project supervisors also gives you an entirely new perspective. Instead of relegating you to merely paying invoices, this model lets you interact with other people involved in the process such as suppliers, resulting in a more nuanced understanding. However, you do need to follow the detached house market closely from a slightly different perspective from the very start of the project, not to mention when you’re getting ready to set a price and sell the results.
The moment of truth arrives when the potential buyers appear, expecting a home designed and built to their tastes and for their personal things, pets, hobbies, and preferences. This is when an architect’s visions of customisation and general applicability are put to the test. The ABC houses received very encouraging feedback from buyers in the sales phase, and each home found happy new residents quite swiftly.
CREDITS
Architect Office Skammi was founded in 2003. Skammi specialises in the design of detached houses and other low-rise homes, including the “Skammin talo” (Skammi House) at the 2014 Jyväskylä Housing Fair. Partners Satu Ratinen and Markku Sonninen.
Satu Ratinen, Chief designer, Architect SAFA (1997, Aalto University, formerly the Helsinki University of Technology). Experienced designer of daycare centres and low-rise homes. Particular interests include the interplay between municipal zoning and building design, interaction in the architectural design phase, the circular economy, slow design, and community art.
Markku Sonninen, Architect (1986, Aalto University). Municipal zoning experience in the town of Siilinjärvi 1987-2005. Has had own design firm from 1977 to 2005, joined Skammi Oy in 2006 to design daycare centres and low-rise homes. Builds homes for himself alongside his design work.
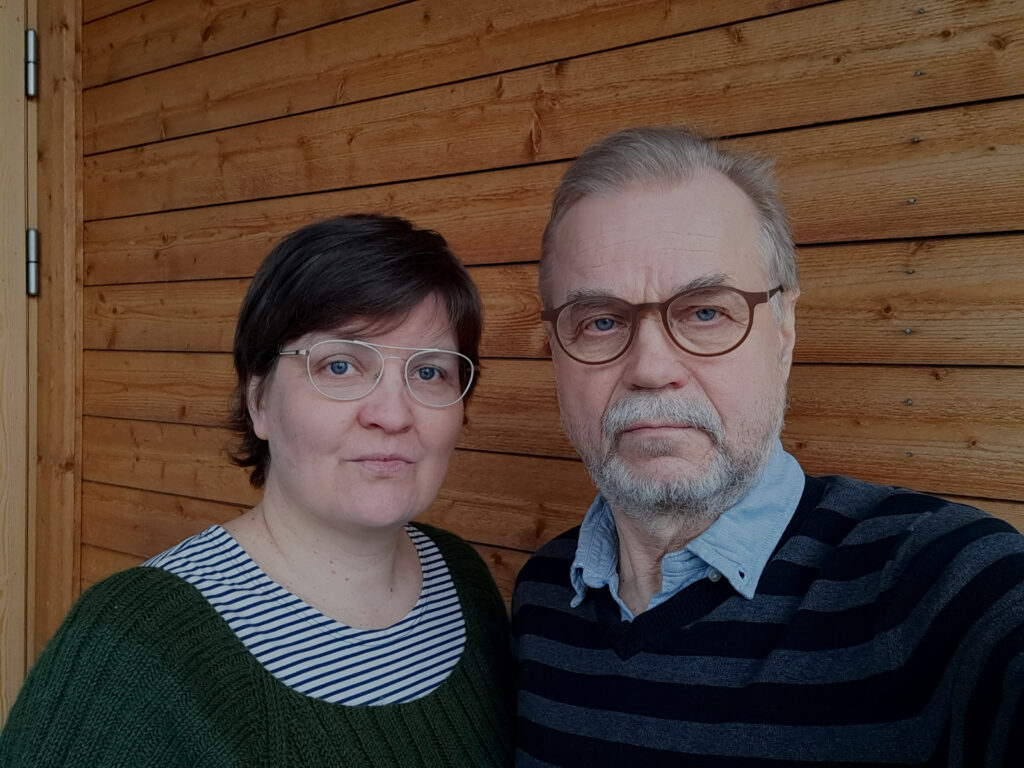
Project in brief
The ABCs of houses
- Location | Espoo
- Constructor/Client | Satu Ratinen and Markku Sonninen
- Year of completion | 2022
- Floor area | 383 m2
- Total area | 467 m2
- Volume | 1 378 m3
- Architectural Design | Skammi Oy, Arkkitehdit Satu Ratinen (SAFA), chief designer and Markku Sonninen
- Structural design | Insinööritoimisto Jukka Silver, chief structural designer and vice president Antti Niinikoski
- HVAC design | Henrik Kemppainen Oulas Oy, KVV-valvoja Mikko Halonen Ormit Oy
- Electrical design | Lyyraks Oy, Vesa Lyyra
- Interior design | Satu Ratinen and Markku Sonninen
- Other designers and specialists | Mitek Oy, Palola&Piispanen Oy, Uudenmaan maanrakennussuunnittelu Oy
- Other contractors | A-perustus Oy (Potius Oy), Mjo-katto Oy, Lattiamies Oy, Uudenmaan lämpömestarit Oy, Louhintaurakointi Noopila Oy, Ekovilla Oy
- Wood component supplier | Valwood Oy, Siparila Oy, Pohri Oy, Nerkoon höyläämö Oy, Stark Oy, K-rauta
- Other materials | Stark Oy, K-rauta, Skaala Oy, Rudus Oy, Heatco Oy, Keittiömetsä Oy, Meltex Oy, Haltex Oy, Talokaivo Oy, Kyky-lasi Oy, Ruukki Oy, Ido Oy, Pukkila Oy, Elotec Oy, Oras Oy, Hansgrohe Oy, Lapetek Oy, Weber Oy, Onninen Oy, Siemens Oy, Vilpe Oy
- Photographs | Sami Saastamoinen
- Text | Satu Ratinen and Markku Sonninen