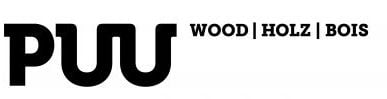
Competitiveness improvement projects for wooden multi-storey construction
Read the article in Finnish: Puukerrostalorakentamisen kilpailukyvyn kehittämishankkeet
“Wood construction is evolving rapidly and attracting widespread interest. Support is also available to further promote wood construction.”
These are the closing words of the research report “Elinvoimaa ja kestävyyttä teollisella puurakentamisella” (Vitality and Sustainability with Industrial Wood Construction) published by the University of Vaasa in spring 2021. Based on the study’s interviews, although wood construction is often perceived as expensive, cost efficiency and cost competitiveness are also a potential driver of wood and CLT construction in industrial construction.
– For modular construction in particular, speed and the benefits stemming from standardisation were often highlighted in discussions related to the research, says Asta Salmi, Professor of Business Administration.
This article presents a few current wood construction development projects as well as operators in the wood construction field. Most of the projects have received funding from the Finnish Ministry of the Environment’s Growth and Development from Wood program.
Productivity leap, case Kuokkalan Kalon
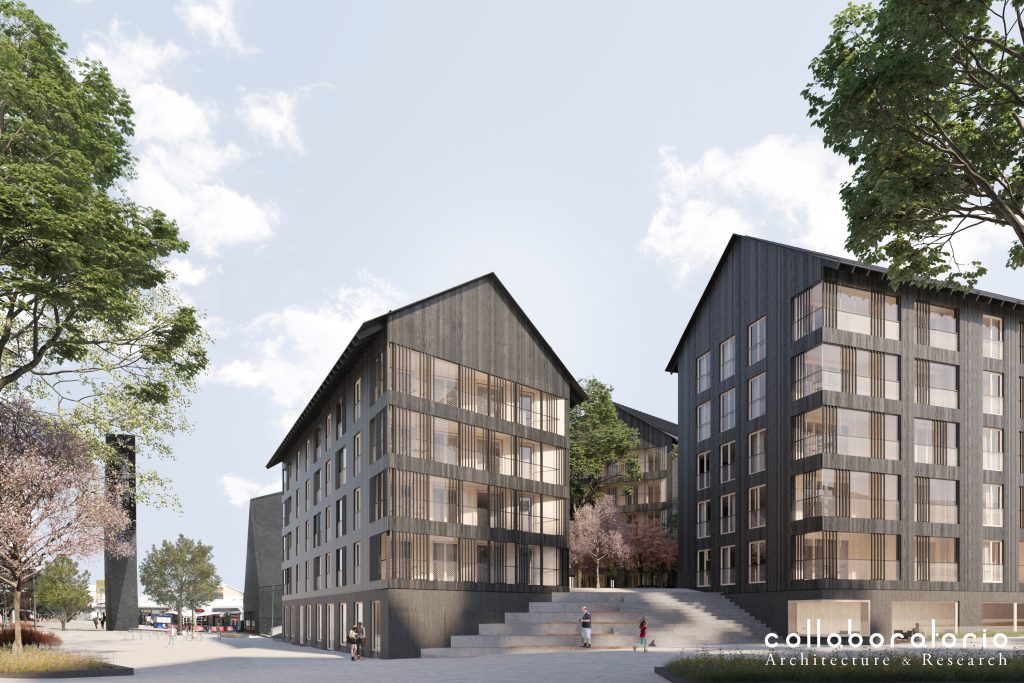
JVR Rakenne Oy is the market leader in volumetric element construction. The company took its first steps into the market in the Puukuokka project and has seen continued growth thanks to its extensive R&D. Starting out with volumetric element installation in 2015, JVR has since added a design office and their own element production plant to the Group. In 2020, JVR Rakenne took part in the Kasvu Open project for growing companies and did well in the Growth Path of Wood Construction category.
They are now part of the Tuottavuusloikka (Productivity Leap) project funded by the Ministry of the Environment, with Kuokkalan Kalon serving as their case project starting this autumn.
Tuottavuusloikka is a research project that seeks to develop wood construction productivity in cooperation with the University of Tampere and Timber Bros, among others. The aim is to bring the Lean thinking developed for factory conditions to actual wood construction sites, which is a challenging but interesting premise. The project promises “openness and transparency in costs and choices”.
Arttu Suuronen, CEO of JVR Rakenne Oy, says that they have high expectations for the Productivity Leap project.
– We have invested a lot of work and money in this project. Our design process is already seeing improvements, but factory production and site operations also have huge potential.
In May, they handed over their most demanding project to date, HOAS Tuuliniitty. A surprise for Suuronen was how much slower construction was with the increased height.
– The processes need to be different for high-rise construction, and for Tuuliniity these needed to be developed quickly.
Although the site was JVR’s most challenging to date and not its greatest financial success, the company wants to build more and to go higher. JVR is growing swiftly with net sales doubled from the previous year and likely to double next year as well.
Hungry for more. Some projects have already been successfully completed, but there are even more in the pipeline.
JVR has its foot in the door of the Helsinki construction market thanks to the Re-thinking Urban Housing program, where the company has several upcoming projects. In the Asuntoreformi block in North Pasila, the challenges stemming from architectural requirements and traffic noise will be solved jointly with Asuntosäätiö and A-Kruunu. In the Jätkäsaari circular economy block, the intention is to combine CLT volumetric element construction with circular economy products such as recycled concrete pillar beams to build the underground parking garage.
– The circular economy is an endless vista of potential research, says Suuronen.
The Kuninkaantammi project of the Yrjö and Hanna Foundation has a solid wood exterior wall without additional insulation. However, the energy efficiency requirements in the plot handover conditions pose a challenge for the builder, and property-specific energy production will need to be enabled.
They are also looking for a plot for a self-financed project, where the goal is to leave as much visible wood as possible on apartment interior surfaces built with R90-class load-bearing structures.
Successful projects in recent years include Mannisenrinne, Hoas Tuuliniitty and Kuopio’s Puukeila. Kuokkalan Kalon and Julkula in Kuopio are under construction.
The Julkula project in Kuopio, which JVR is delivering as a socalled Lakean Omaksi turnkey contract, is a true leap in productivity.
– When the design, production and installation of the elements are all in your own hands, you are the master of your own success, says Antti Erola, CEO of JVR Plus Oy.
The forging of the Sampo, case TOAS Hippos
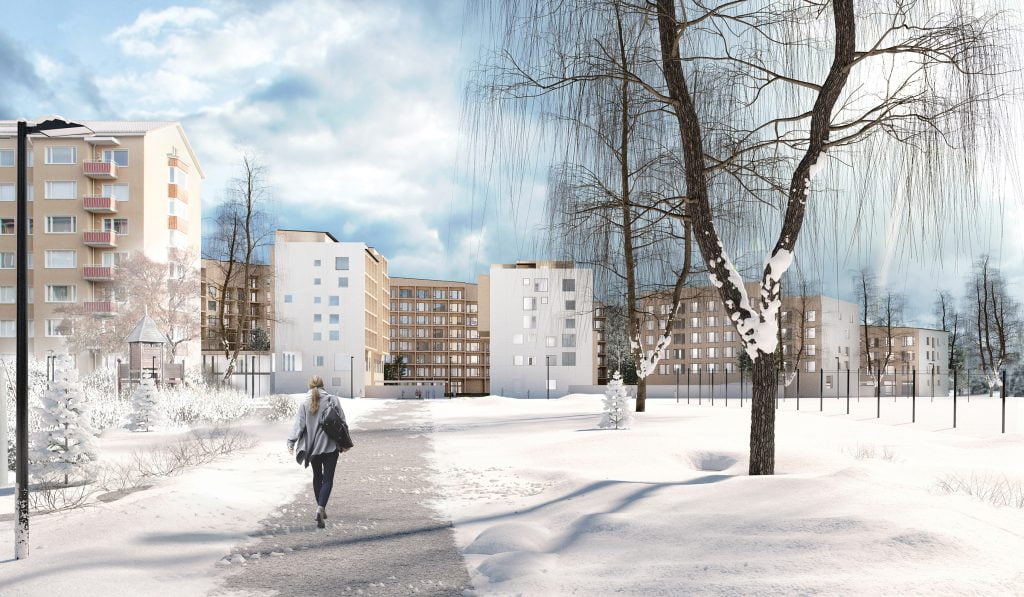
The development of TOAS Hippos began in 2016, and the alliance kicked off the planning process a year ago. Sustainable development was the goal from the very beginning, so the decision was made to build with CLT volumetric elements.
TOAS Hippos is based on the Sammon taonta (Forging of the Sampo) development project, which is looking for savings of 20 % in CLT volumetric element construction. This means that after this project, Elementti Sampo hopes to quote a 20 % lower investment cost to the developer of a wooden apartment building project in autumn 2022.
Sauli Ylinen from Elementti Sampo says that several potential development targets have already been identified since the project started last spring.
– The steps required to achieve savings will be described in the final report.
The introduction of Lean thinking at the factory and, where possible, at the construction site with other operators is a significant factor. Ylinen is particularly inspired by how the project’s participants are all learning through working together.
– Working and searching for solutions together with Hartela, A-Insinööri and TAOS, we all learn a huge amount about building construction as a whole.
Sami Pajunen from Tampere University is involved in the Forging of the Sampo and Productivity Leap projects. Professor Pajunen, whose work has been praised in both projects, has set out to identify design bottlenecks and find out where design time is spent. Once the bottlenecks are identified and resolved, the researchers will make recommendations for streamlining the design process. The design guidelines for stiffening a building, for example, are currently too vague. As an end result, the Productivity Leap and Forging of the Sampo projects have also promised to provide indicative 2D images for volumetric element construction.
At the graduate school of industrial wood construction at Tampere University, Harri Sivu is studying the overall process of wood construction and the relationships between project operators. Sivu strives to find the best possible network model to improve the competitiveness of wood construction and to provide the network’s operators with optimal roles where risk and return are in balance. His work will propose new business and contract models, but won’t forget financing models. The research project will run for five years, and Hippos is one of the project case studies.
Pukki project, case Kuusikko
Arkta has a history of wood construction that began just over ten years ago in Heinola when it was Rakennusliike Reponen. Arkta builds from balloon frame large elements and has succeeded in retaining its market share despite the competition from solid wood constructors.
Operating in Pirkanmaa, one third of the apartments being completed this year by Arkta Rakennus will use wood. The company is currently building Kuusikko in Tampere: the largest wooden apartment building site in Finland. Part of an extensive Tampere University Pukki research project, Kuusikko serves as a test case for researching business challenges and opportunities in wooden apartment building construction from a real estate development perspective. The project is funded by Tampere University, the City of Tampere, the Finnish Ministry of the Environment, ARA (the Housing Finance and Development Centre of Finland), both developers, the main contractor, the wood element supplier, and the material supplier. Juha Franssila has worked on the two-year project as a dissertation researcher. The project examines value creation associated with responsible real estate development, wooden apartment building construction, the circular economy, and which aspects stir investors’ interest in wood construction in particular.
– We can already see now that responsibility, the potential of new construction techniques, and tightened regulatory requirements all make wood construction more attractive. Responsibility is a widely held value among customers, and wood construction productisation can add new attractive growth prospects to the business. The third unavoidable reality is that regulatory requirements on construction industry emissions will be tightened. Constructing multi-storey buildings from wood offers one possibility for resolving these challenges, says Franssila about the research results so far.
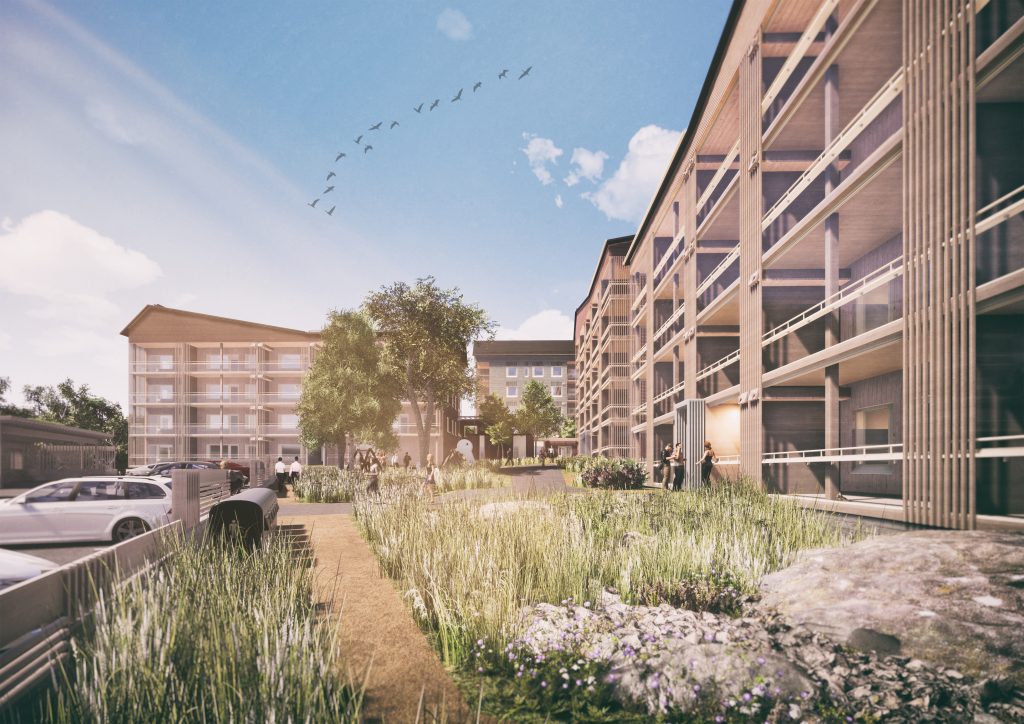
The project has produced two theses: Lauri Alkki, 2021, Puukerrostalorakentamisen kiertotalousverkoston toiminnan kehittäminen (Development of circular economy network operations for wooden apartment building construction) and Veera Simola, 2021, Puukerrostalot osana vastuullista kiinteistöliiketoimintaa (Wooden apartment buildings as part of responsible real estate business operations). Franssila’s article is expected to be published next year.
Timo Ristamäki from Arkta Rakennus sees the EUR 25,000 that the company invested in the development project as money well spent.
– Working with customers, the city, Ara and the university to develop and push wood construction forward is very important, says Ristamäki.
– When we sit at the same table, we achieve a common understanding of everyone’s needs and can more easily steer our own work in the right direction. Perhaps soon we will even have our own wood structure production. The group has strongly emphasised wood construction and all kinds of frame solutions are regarded as possible.
Responsibility is reflected in condominium prices
The selling prices for wooden apartment buildings in Helsinki are almost 9 percent better than for other materials. Trends in prices are driven both by environmentally conscious consumers and by investors, say researchers at Aalto University. This is the first known instance in the world where the building materials themselves have demonstrated a green price signal.
– Wooden apartment buildings sold in Helsinki between 1999 and 2018 had a price that was 8.85 percent higher on average than those made with other materials, says Ilmari Talvitie, a doctoral student.
The researchers analysed statistics from Suomen Kiinteistönvälittäjät ry (the Association of Real Estate Agents) on sales in Helsinki, Espoo, and Vantaa. Wooden apartment buildings made up an average of 2.23 percent of these sales. Because prices always have several underlying components, the researchers used regression analysis to isolate the other variables, leaving prices as the item being compared.
Professor Seppo Junnila clarifies that the location variable in particular would make comparison impossible without regression analysis.
– Wooden apartment buildings were cheaper on average in the statistics at first glance, but the numbers in Helsinki were in favour of wood once location was factored out. In practice, this means that the price per square metre differed by nearly a tenth between similar apartments in wooden and concrete buildings in the same area, he says.
In Espoo and Vantaa, wood had no discernible effect on prices in the comparison. Researchers think that this is in part because wooden apartment buildings in Helsinki tend to be built in areas with lower prices. In such areas, the green price signal, meaning a willingness to pay more for environmental values, is easiest to see – and perhaps not even possible in other areas.
– Consumers may appreciate environmental aspects and also want to signal their green values to others. In the study, we found that wooden buildings have a greater than average tendency to be located in areas of lower socio-economic status, which in turn means that wood is a factor that increases the price, says Talvitie.
– Young students looking to buy their first apartment may not have a lot of money, but they want to consciously invest in environmental issues. On the other hand, the big construction companies have not yet seen a business opportunity in wood construction, which means they have not dared to build such buildings in more expensive areas, says Junnila.
The Finnish Ministry of the Environment aims to have 45 percent of new apartment buildings be made from wood in 2025. This represents a huge leap from the current situation, and according to the Aalto researchers this will not happen without a clear market mechanism.
– Legislation alone is never enough; rather, people have to want to live in wooden residences and companies have to see business opportunities in them, Junnila concludes.
Companies building single-family homes are already visibly interested: the proportion of log houses has risen from 11 percent to 27 percent in ten years, despite costing a tenth more than basic wooden houses.
Source: Aalto university
NCC development projects
NCC originally started building wooden homes because it simply had no choice: all available plots in Turku had a wood frame requirement mandated by the city. In Linnanfält, five wooden apartment buildings were constructed with different structural systems and different suppliers’ products. Once they were complete, Rakennuslehti magazine’s November issue summed up the realities: “Practice doesn’t make perfect – wood construction similar to Turku’s Linnanfält is still 10-20 percent more expensive than concrete.” NCC now has two projects planned with Elementti Sampo.
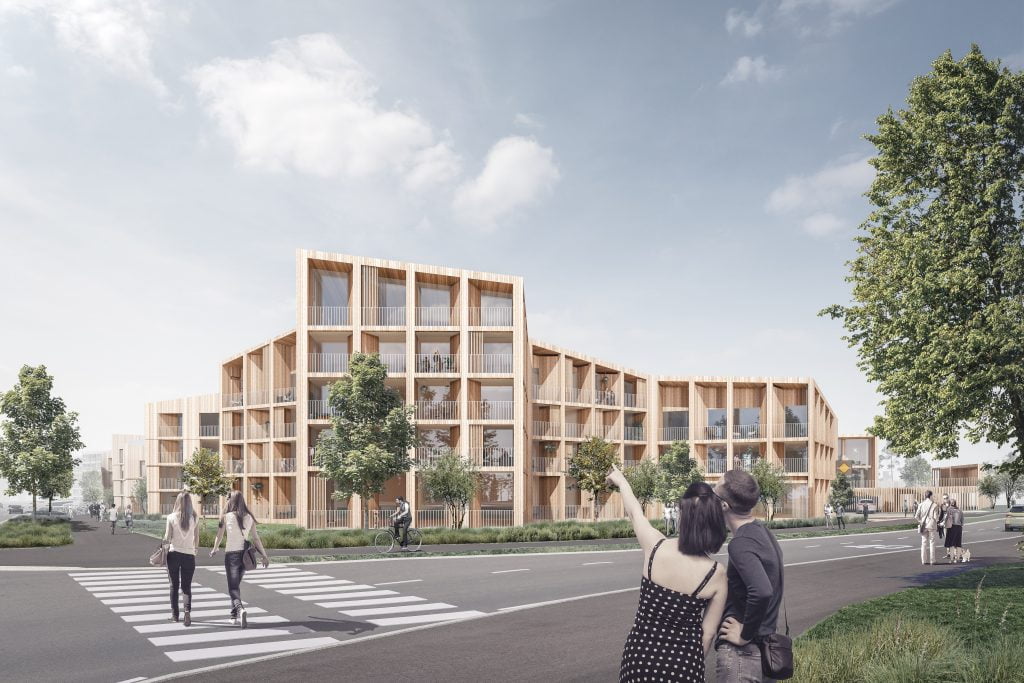
They won the Järvenpää Sävelpuisto project with their use of CLT volumetric elements, although neither the municipal plan nor the developer required it. The building will have 11 corners, which is not a problem according to project development manager Juha Heijala.
– Volumetric elements allow everyone to take a new approach.
For NCC, wood is a material like any other, but we do consider it worth exploring. After Linnanfält in Turku and a few schools, the company wanted to expand into CLT volumetric element construction. The company is also seeking productivity improvements with each project.
NCC is known for having the traditional construction process down to a tee, but now it needs to learn something entirely new. However, plenty of knowledge can be carried over from traditional construction.
– While the Järvenpää Sävelpuisto project is ongoing, we are also developing a new co-operation model with Elementti Sampo. We want to change up the typical procurement model used in volumetric element deliveries, says Juha Heijala.
The new apartment building concept of the City of Helsinki
The City of Helsinki is developing wood construction for several reasons, particularly due to it being suitable for infill construction and for increasing competition among contractors. The City believes that wood construction operators could bring much needed additional capacity to housing production and also a little healthy competition.
With the wood construction businesses in mind, the city is now working on a prototype wooden apartment building that suits infill construction. Much like the “Helsinki” detached house ten years ago, Helsinki’s housing production is now developing the wood-structured Make 2.0 building in line with the city’s goals. The project aims to design and build a cost-effective, sustainable, and visually pleasing wooden apartment building that can be “duplicated” with suitable variation for infill construction. The concrete “Make” apartment building, developed in housing production in 2014–16 and built in 2019, serves as the basis for the design and is being developed to suit wood construction and current regulations.
The replication-friendly concept can streamline the planning and construction processes for infill construction and help make small-scale infill construction more viable. Like its predecessor, the “Helsinki” detached house, the concept is intended to be suitable for production by house manufacturers. The idea is to create an attractive product for builders and contractors by standardising some of the prototype’s building components and quality guidelines. Cooperation with ARA (the Housing Finance and Development Centre of Finland) will expand the project’s impact nationwide.
– What makes the project particularly rewarding is that ARA sees the building’s potential in the construction of affordable housing nationwide, says Ulla Kuitunen, who was still the Development Manager for Housing Production in the City of Helsinki at the time this article was written.
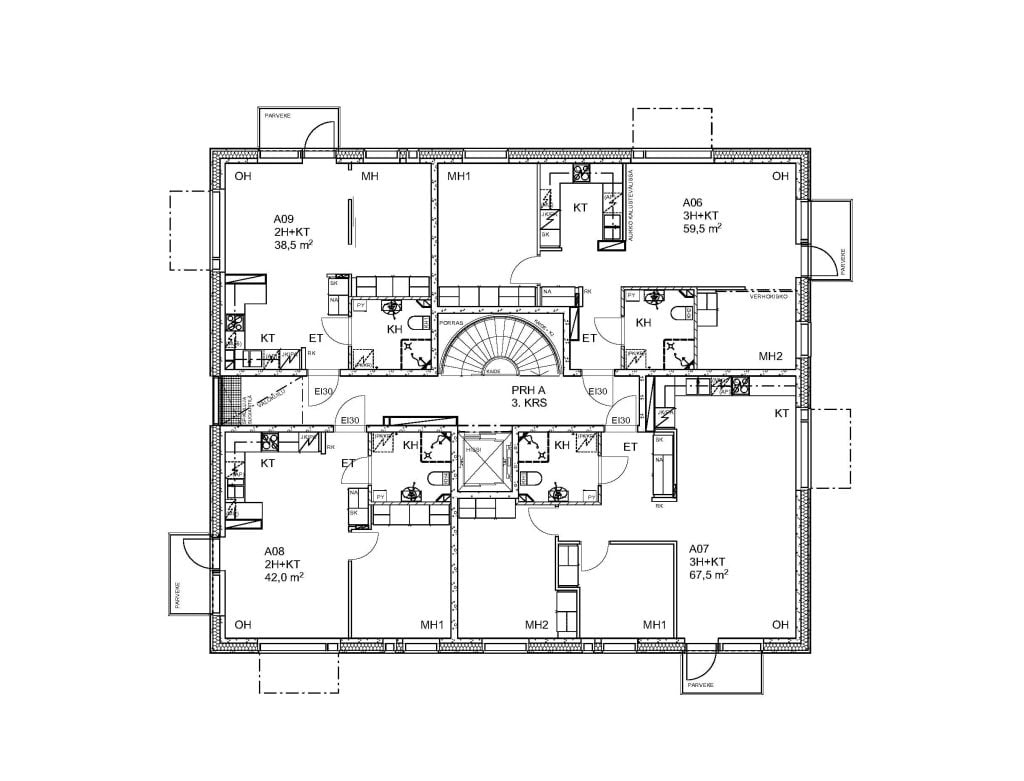
Text : Anu Turunen