
Dovetailed massive wood board elements for multi-story timber-framed buildings
Multi-story timber-framed buildings have been a new promising industry with a high capacity for supporting the bio-economy and technologically refurbishing construction sector. They can contribute to social well-being both within primary production and within wood-based value chains. In this industry, as a growing market in Europe, EWPs (Engineered wood products) e.g., cross-laminated timber (CLT), glue-laminated timber (Glulam), laminated veneer lumber (LVL), Massiv-Holz-Mauer® (MHM) have had an important position with the production capacity of more than 5 million cubic meter/year.
Along with EWPs, non-adhesive building boards have been developed. Due to new research, the potential of the ‘innovative dovetail concept’, inspired by one of the oldest joining techniques, could be further exploited in building construction, for example, in multi-story timber-framed buildings.
Authors: Post-doctoral Researcher Hüseyin Emre Ilgın, Professor Markku Karjalainen, Tampereen yliopisto
Read the article in Finnish here.
Adhesives help protect the wood, and make the structure strong, but raise also concerns
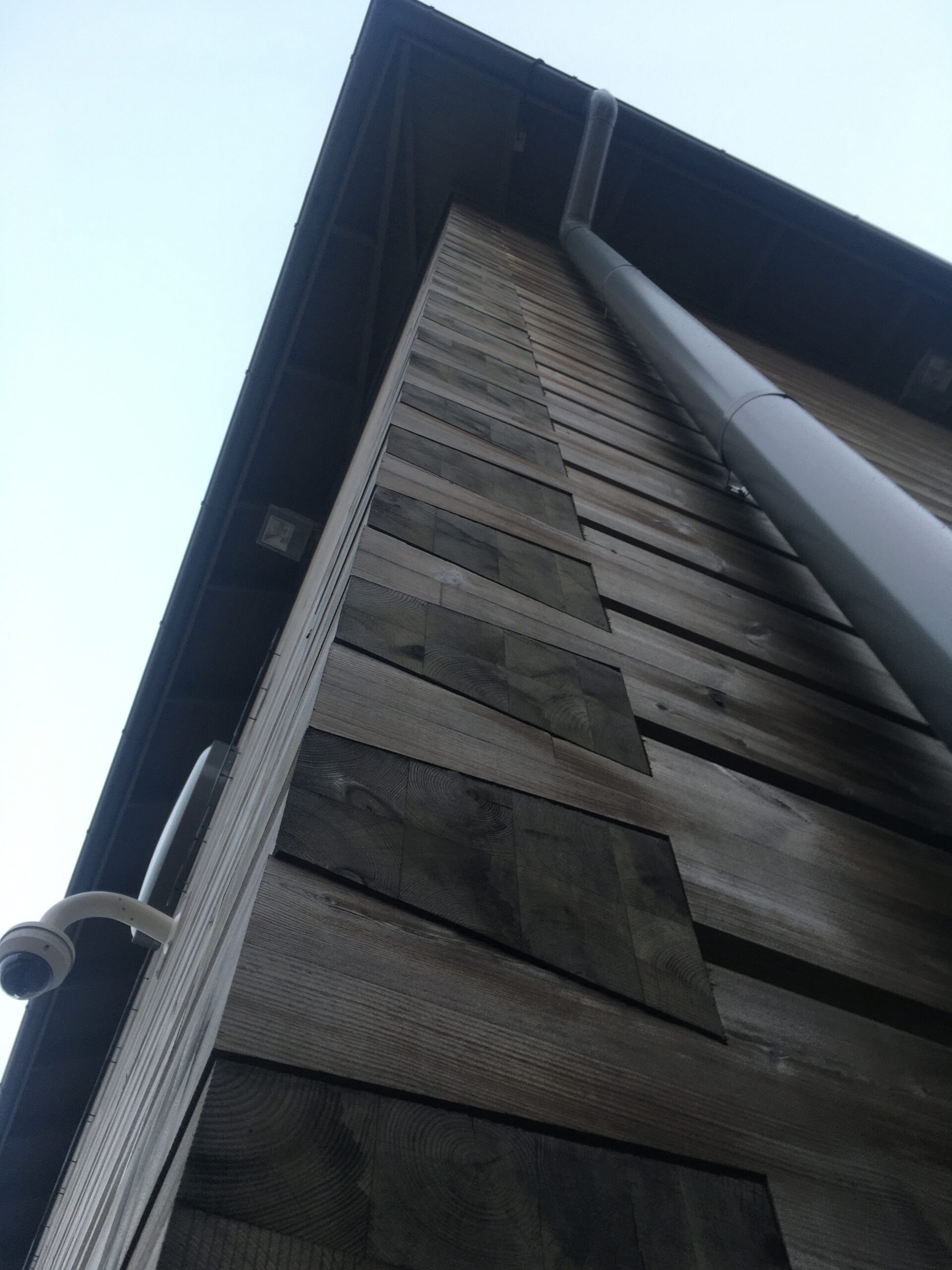
Adhesives in EWPs help protect the wood, make the structure strong and light, and prevent shrinkage and expansion caused by natural humidity. Adhesives and metal fasteners play a critical role in the content and connections of EWPs. EWPs have uniform strength and stiffness, as well as low carbon and high thermal insulation. EWPs have even been used in buildings over 80 meters high, such as Ascent (Milwaukee, 2022) and the 85-meter Mjøstårnet (Brumunddal, 2019) (Wood magazine 3/2023 “Tall wooden buildings: potential, benefits, challenges, and prospects“).
However, the current widespread use of adhesives causes challenges for the recyclability of wooden parts. In particular, if wooden parts are burned at the end of their life cycle, gases harmful to the environment and human health are released into the air.
Environmentally friendly bio-based adhesives have been developed and the goal of the industry is to raise the properties of environmentally friendly wood adhesives and their synthetic competitors to a better level, but their competitiveness is not enough yet. So far, the relatively weak water resistance and bond strength of bio-based adhesives have held back wider adoption. The weakness of the metal fasteners used in EWPs is also that they complicate the disposal, reuse and recycling of the products. Their poor water resistance and bond strength are the main constraints in replacing petroleum-based wood adhesives with bio-based adhesives. On the other hand, metal fasteners, as well as adhesives, are of great importance to EWPs, but they harm the end-of-life disposal, reusability, and recyclability of EWPs.
The solution is a dovetail joint in a solid wood board elements
The history of the dovetail technique goes back to before Christ. Some of the earliest known examples of this technique are ancient Egyptian furniture embedded in First Dynasty mummies, stone pillars from Temples in India, as well as in Chinese ancient architecture. In Europe, the dovetail joint is also called a swallowtail joint, a culvertail joint, or a fantail joint. Early residential constructions with timber-framed structures, dating from the 13th century, consisted of mortise and tenon joints, strengthened with wedges, notched joints with tenons, and dovetail joints.
Throughout history, there are four most prevalent types of joints to be employed to fit walls together in building construction:
- double notch,
- half notch,
- “the lock”, also called a “German” or “Saxon” joint,
- full dovetail (fishtail) notch
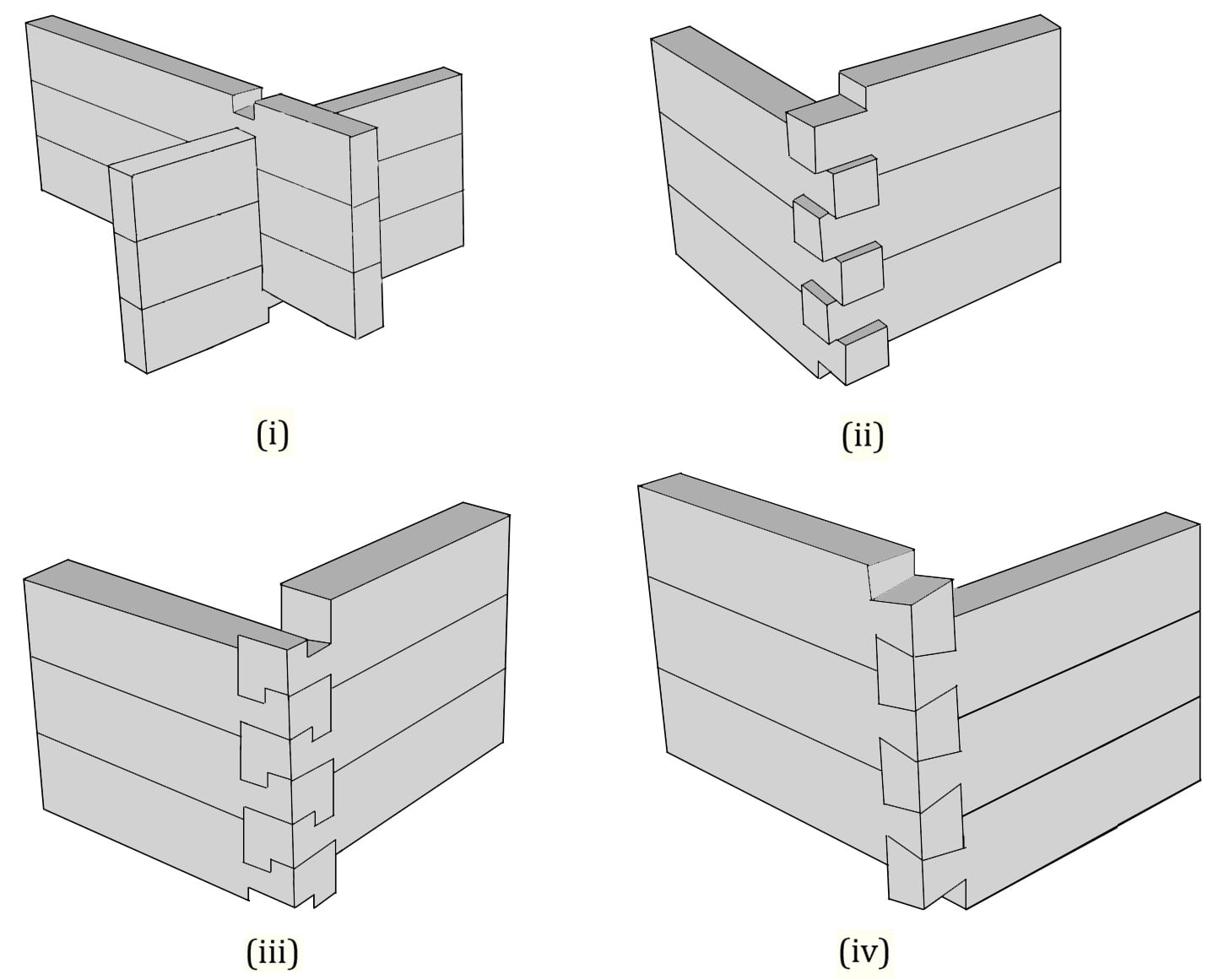
These wood-to-wood joints do not contain any glues or metal fasteners. Environmentally friendly joints have been widely used in the construction industry until the middle of the 20th century, when construction changed and the inefficiency of production combined with increased labor costs made the joint type uncompetitive in new markets. Today, the development of CNC woodworking technology has made wood-to-wood joints cost-effective to implement. Alongside the CLT board, DWBE (Dovetailed Wood Board Elements) made with dovetail joints without adhesive and metal fasteners has been developed.
From DWBE, a replacement for EWPs for the global market of wooden apartment building construction
An experimental comparative fire/charring performance study with CLT was carried out at Tampere University Fire Laboratory in April 2022. Test specimens of 200 mm thickness, 950 mm width and 950 mm length for CLT and DWBE were tested according to EN 1363-1. The charring performance of DWBE was found to be very similar to solid timber. With the tested lamella thickness, DWBE connection was able to effectively prevent the char fall-off. CLT specimens had a clear increase in the charring rate value due to the char fall-off of the first lamellae layer.
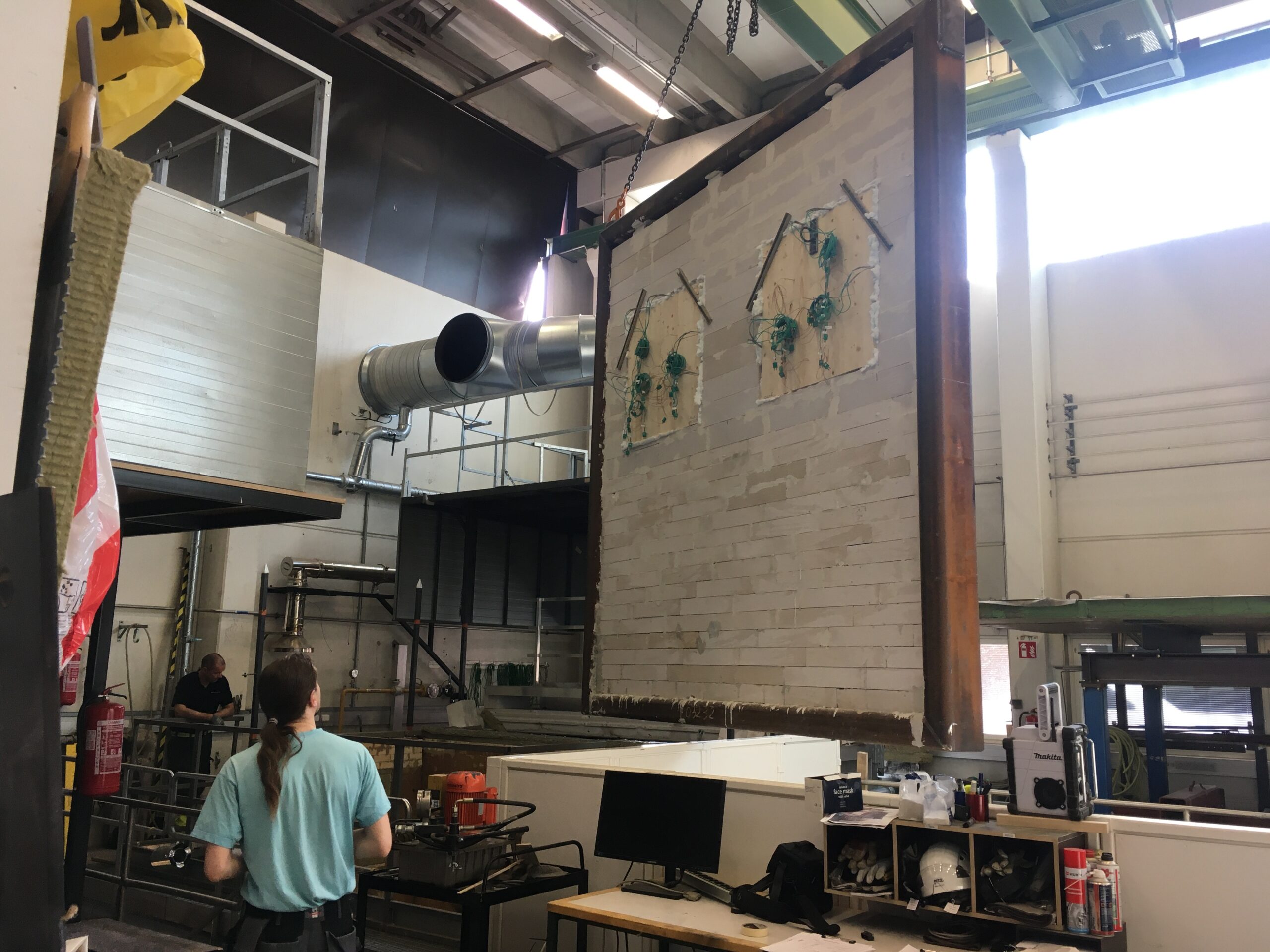
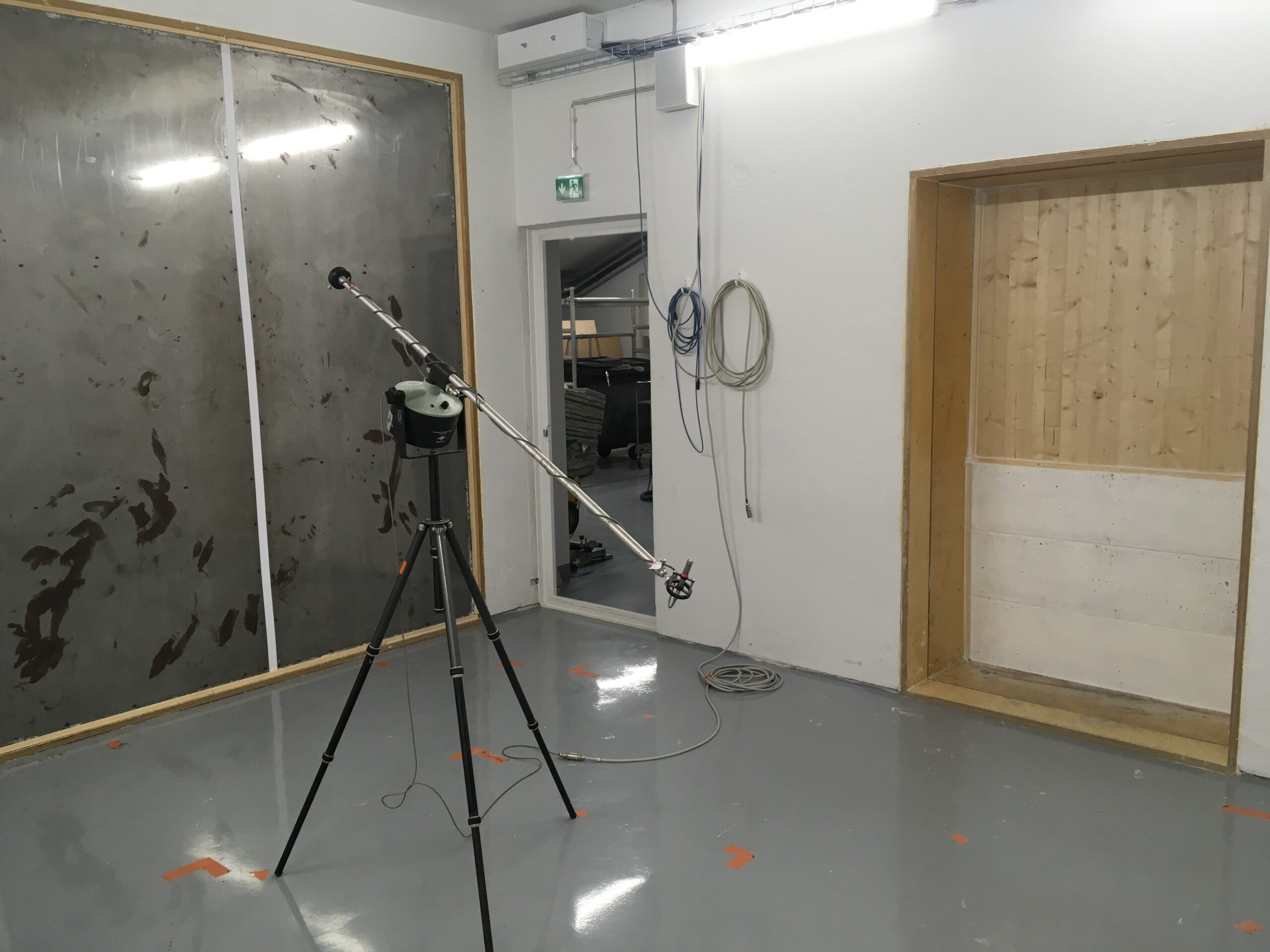
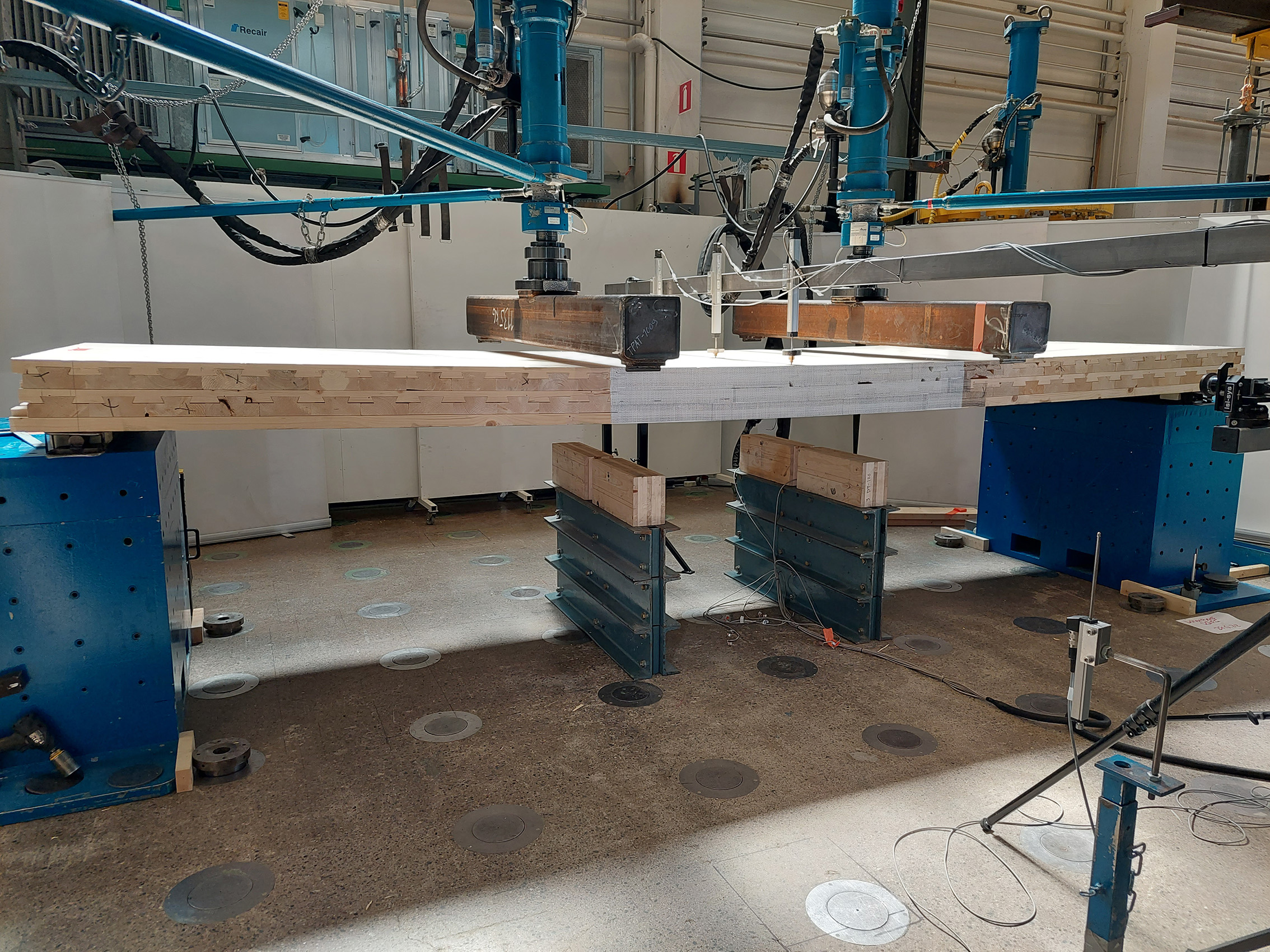
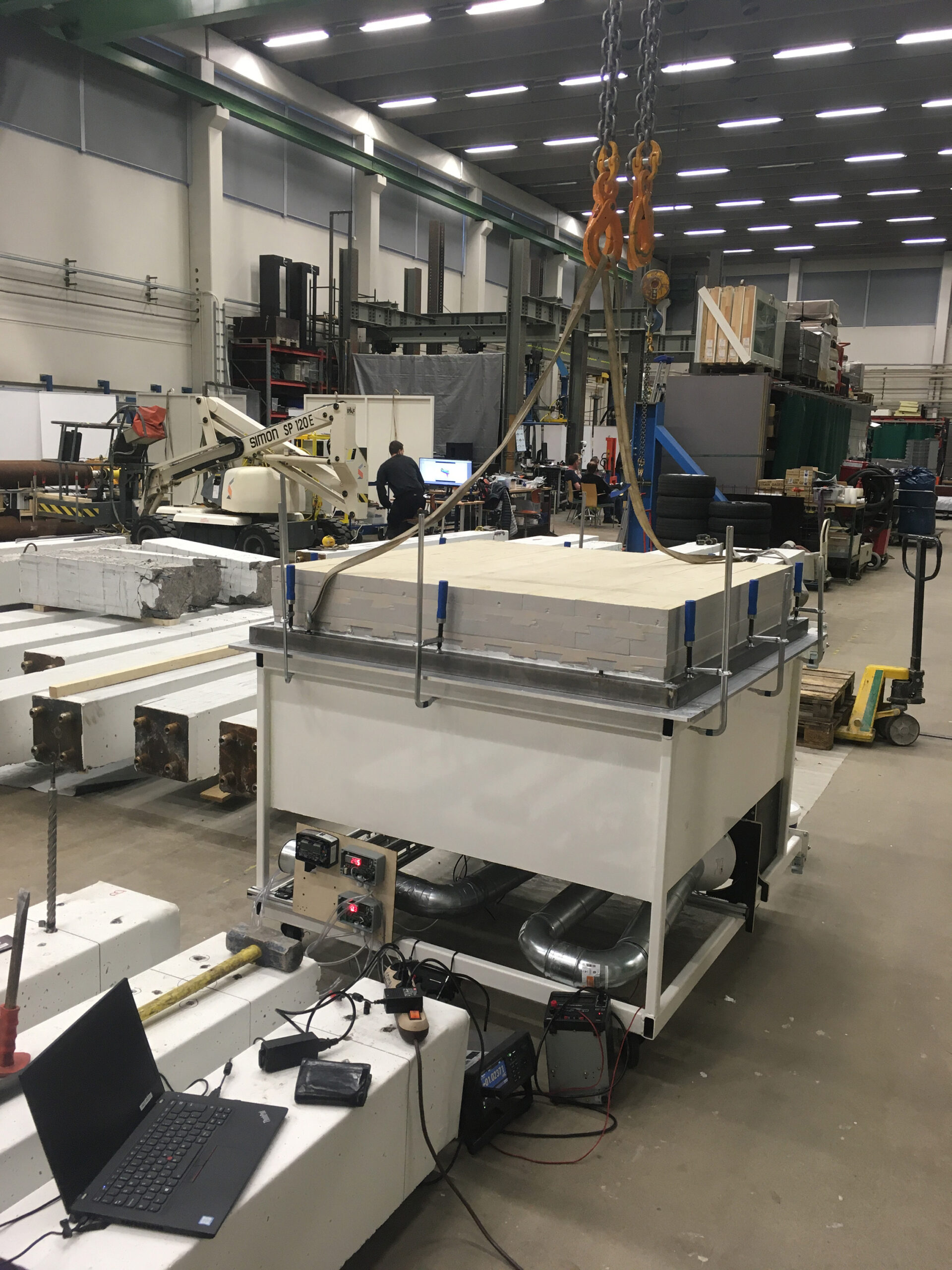
In May 2022, a comparative evaluation was conducted at Turku University of Applied Sciences Acoustic Laboratory, examining the airborne sound insulation capacities of both DWBE and CLT. Test specimens of 200 mm thickness, 1160 mm width and 1190 mm length for both CLT and DWBE were tested according to ISO 140-3 standards. The results highlighted the enhanced airborne sound insulation performance of DWBE (43 dB) compared to CLT (40 dB).
Moreover, comparative bending tests were performed at Tampere University Structural Engineering Laboratory in June 2022 and March 2023. Test specimens 200 mm thick, 1450 mm wide and 5075 mm long were tested for both CLT and differently configured DWBEs (5-ply, doweled and 3-ply versions). These configurations did not exhibit the desired bending capacity and the design needed to be revised and improved. The new configuration was tested in September 2023 and promising results were obtained. The results of the bending tests will be published after the patent processing.
In November 2022, a study was conducted on the air permeance of 3 DWBE variations, following Finnish building code guidelines stipulating the maximum allowable value of 4.0 m3/(m2h) under certain moisture content conditions at Tampere University Building Physics Laboratory. The dimensions of the smallest test sample were 200 mm x 1160 mm x 1160 mm. When DWBE was exposed to dry conditions such as winter, it experienced shrinkage, leading to an expansion of joint gaps and subsequently. Conversely, in conditions with higher humidity levels, the air permeance of DWBE complied with the Finnish building code.
In the literature, many studies have been carried out on the technological aspects of wood with different construction solutions based on the use of EWPs such as CLT. There is an extremely limited number of research on DWBE, and the literature about ‘DWBE’ is based on inadequate structural analysis and model testing of several types of jointing details rather than even evaluating the performance of a structural component, e.g., a shear wall or a whole structure. This prevents us from understanding the potential to break new ground in multi-story timber-framed building construction, particularly in terms of environmental impact and recyclability, and reduces the ‘innovative dovetail concept’ to the level of connection detail. For this reason, it can be clearly said that there is no research on the use of DWBE in buildings, and this research will contribute to filling this gap.
Due to new research, the potential of the dovetail concept could be further exploited in building construction, for example, in tall buildings.
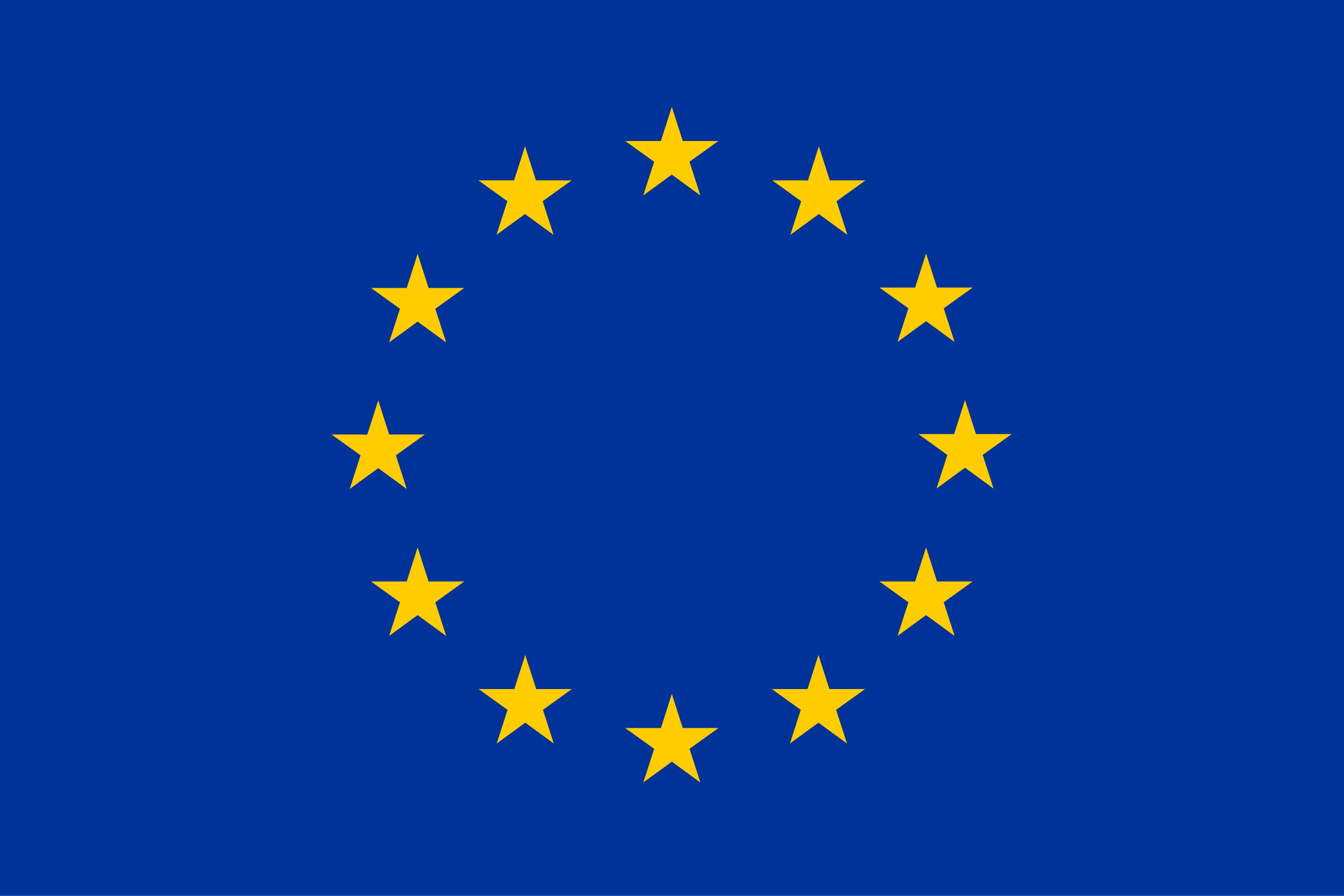
The article is part of a two-year (2021–2023) DoMWoB research project, which has received funding from the European Union’s Horizon 2020 research and innovation programme under the Marie Skłodowska-Curie grant agreement No [101024593].
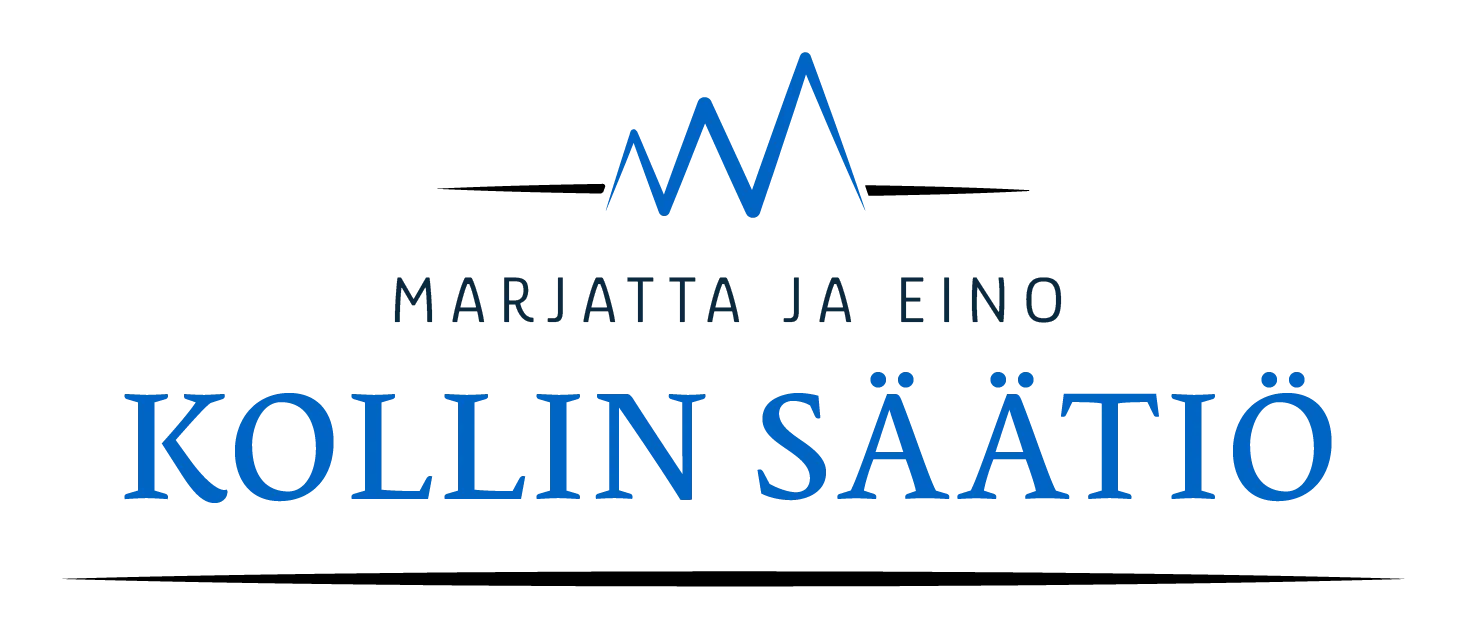
The project has also received funding (60,000 + 33,000 EUR) from the Marjatta and Eino Kolli Foundation for the technical performance tests including fire performance, airborne sound insulation, bending performance, and air permeance, and potential patent application
The project aimed to create higher value-added circular economy opportunities to promote the competitiveness of large-scale industrial timber construction at the local level and to support European climate policy as part of bio-economy and sustainable development. To achieve this purpose, the plan to develop DWBE for multi-story timber-framed buildings for the global market has been proposed as a replacement for conventional EWPs (e.g., CLT, Glulam) by enabling the confidence of its technical performance and suitability within the interdisciplinary collaborations among architecture, structure, and building physics. This study will contribute to the dissemination of DWBE for different and innovative architectural and structural applications, especially in multi-story timber-framed building construction, as one of the key tools in tackling climate change challenges.
CREDITS
Hüseyin Emre Ilgın received his Ph.D. (2018) in Building Sciences about tall building design in Architecture from METU in Ankara. Since December 2019, he has been conducting post-doctoral research on wood construction at Tampere University. Dr. Ilgın worked as a Marie Skłodowska-Curie postdoctoral research fellow on dovetailed massive wood board elements for 2 years between 2021-2023.
Markku Karjalainen works as Professor of architectural construction in the School of Architecture at the Tampere University. He completed his doctoral dissertation in 2002 with the topic: “Finnish wooden apartment building – at the forefront of the development of wooden construction”.
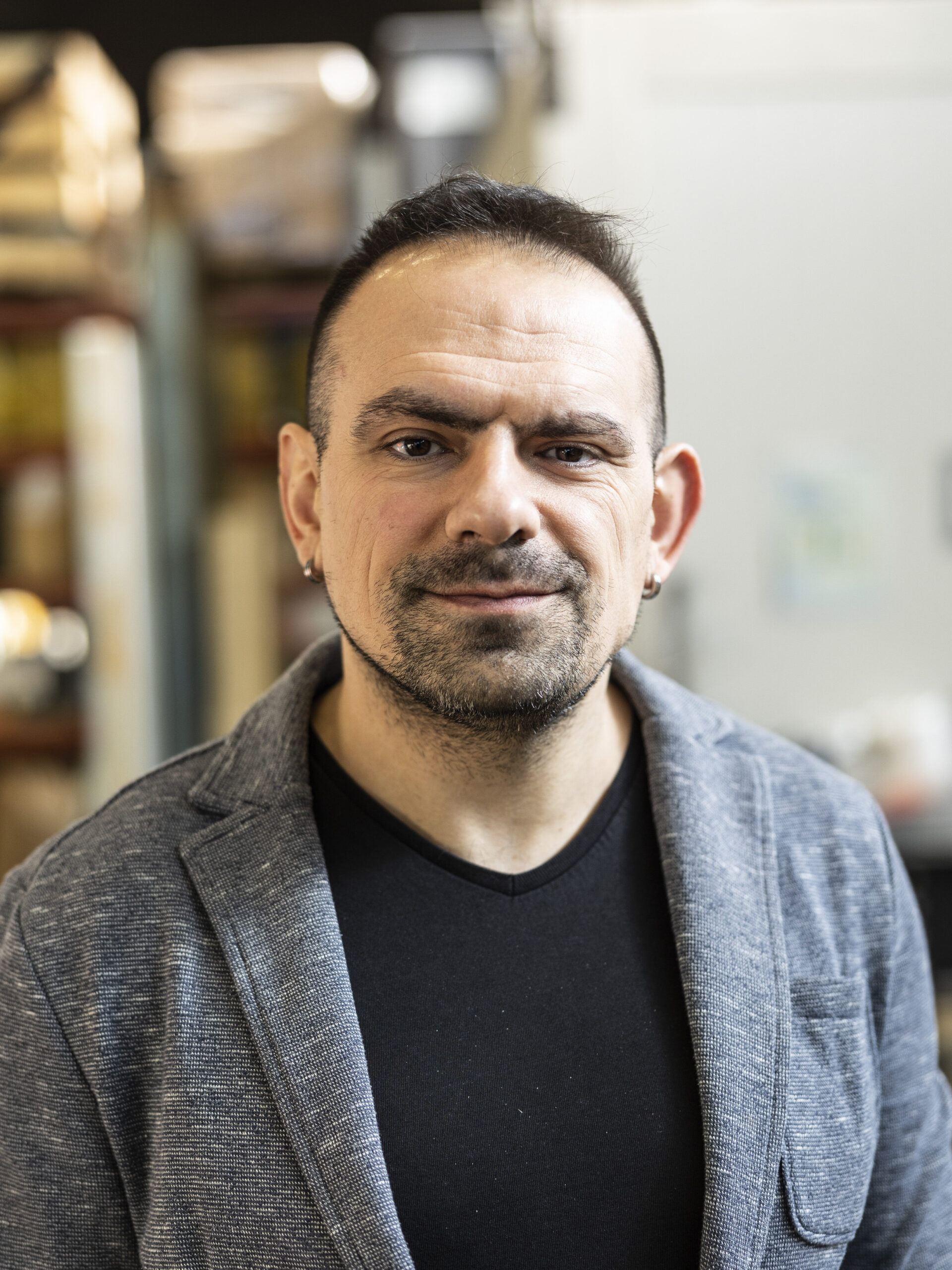
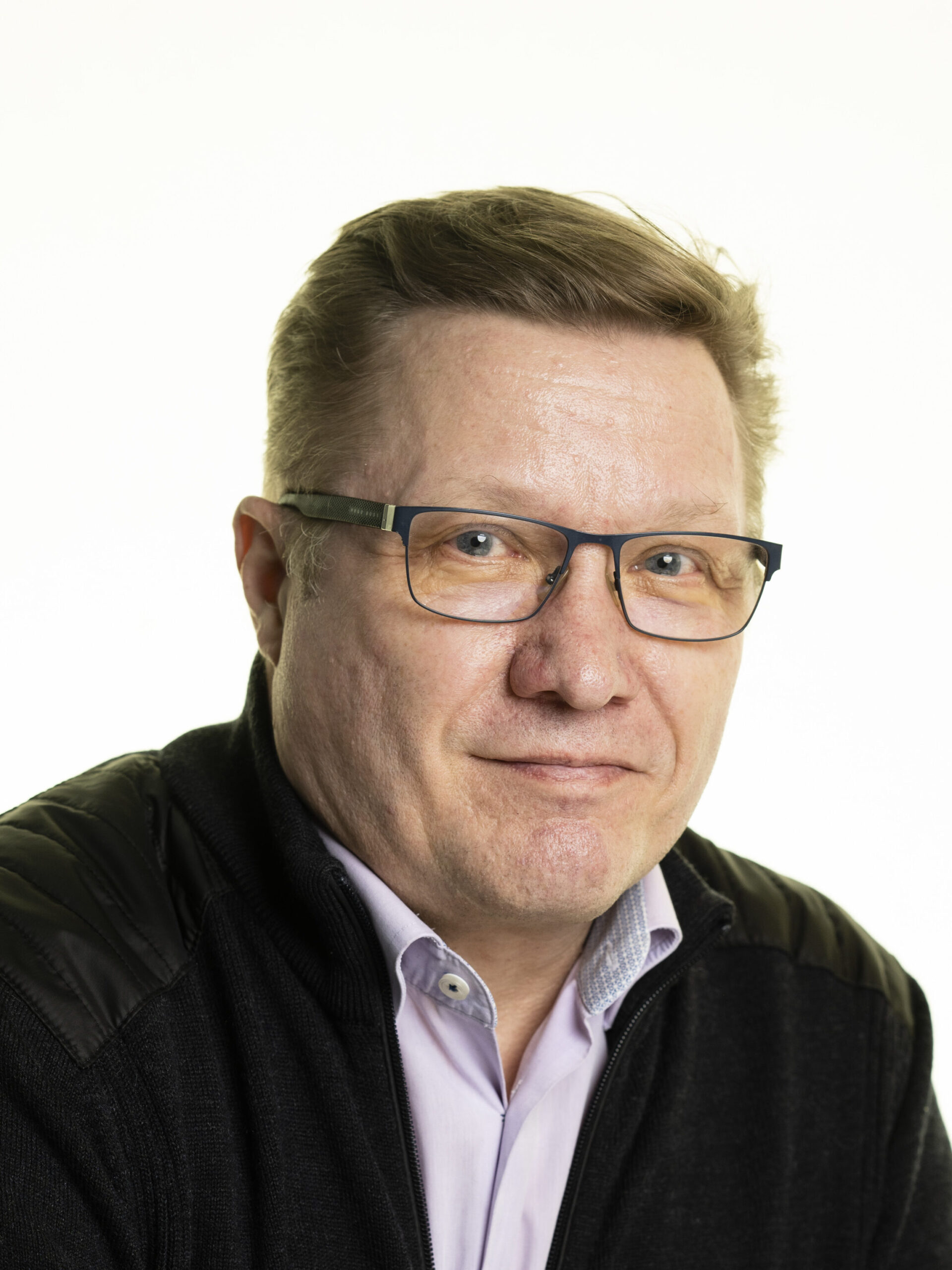