
Reusing salvaged wood in buildings: Non-destructive-testing methods for early-stage decision making
As climate change accelerates, the discourse on sustainability in policymaking, urban planning, and architectural design has increasingly emphasised the circular economy, resilience, and adaptability in the building sector. Recently, the United Nations Environment Program’s (UNEP) asserted that “The construction sector is not on track to decarbonise by 2050” (UNEP 2022), effectively stating that the expected outcome of adaptation strategies and mitigation techniques will not be attained.
Authors: Lukas Seidl, Shammi Keya, Lena Seiwald, Sina Hage, Hermann Huber, Timo Pakarinen
The built environment accounted for approximately 15.3 gigatons of CO2 (37%) of global carbon dioxide (CO2) emissions and an additional 3.6 gigatons of CO2 emissions attributed to the production of building materials (UNEP 2021). Building materials are significant contributors to resource depletion, accounting for 50% of extracted materials and 33% of global waste and water utilisation.
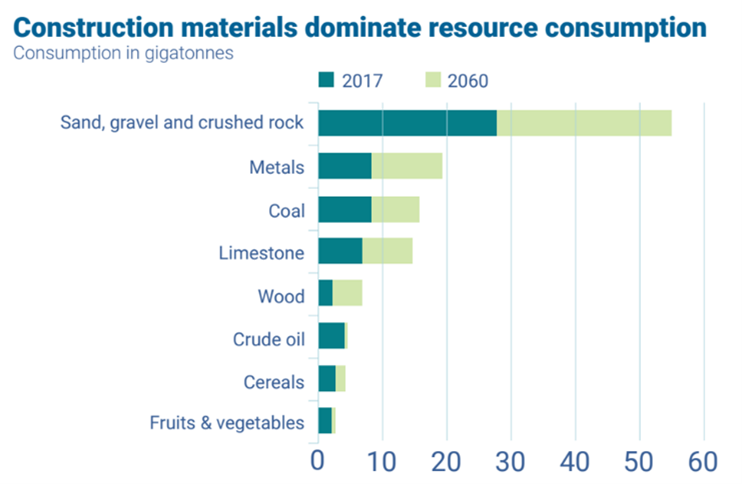
The European Union’s Green Deal underscores the sustainable usage of construction materials as essential for attaining carbon neutrality by 2050. Notably, 17% of the EU’s emissions reduction targets will come from energy efficiency and 15% from demand-side measures and the promotion of material circularity (IEA, 2022). Hence, the construction industry stands on the cusp of a transformative phase, facilitating the circularity of construction materials through adaptive technologies tailored to address contextual challenges and spreading best practices across borders.
Limitations in reclaiming materials from deconstruction
Amidst this paradigmatic shift towards sustainability, materials reclamation through deconstruction emerges as a promising approach. However, a comparative case study on Canada, Germany, and Japan entitled “Barriers for Deconstruction and Reuse/Recycling of Construction Materials,” reveals some common challenges. According to Nakajima, S. & Russel, M. (2014), these issues appear regardless of the specific materials due to the factors listed below:
- Limited appreciation of the reclaimed material’s intrinsic value
- Prevailing industry perceptions of the cost-intensive nature of deconstruction
- Stringent temporal constraints impeding effective deconstruction practices
- Inadequate waste management protocols
- Deficient collaboration amongst subcontractors
- Absence of a robust market for repurposed materials
- Time-intensive material separation processes
- Regulatory constraints hindering the reuse of structural components
- Uncertainty surrounding dismantling costs
- Lack of standardised “best practices”
It can be useful for policymakers to understand these common challenges so that they may better take them into account in their efforts to enhance materials circularity in buildings.
What are the most promising scenarios for reused wood?
In today’s recycling processes in Europe, untreated structural wood from demolished buildings is typically used to produce wood chips for further processing into chipboards and pallet blocks or for use in biomass energy generation. However, until it is downgraded by crushing, used structural wood has great potential for reuse in building structures. One reason for the limited reuse of structural wood from demolished buildings is that the processing into woodchips is already an established and therefore cost-effective recycling method. Another limiting factor is that no standards and certification options have been adopted for the reuse of used structural wood.

Most lumber extracted from construction and demolition across the surveyed counties is reduced to woodchip, regardless of the size or quality of the extracted material. The main uses of these woodchips are particle board manufacture and bioenergy generation. Exceptions to this rule include solid wood, such as glulam, and historical, large section lumber with cultural significance, which are reused directly.
Non-destructive testing (NDT)
Non-destructive testing (NDT) can be defined as the science of testing the mechanical and physical properties or the defects of a piece of material or structure, without having to damage it or alter its integrity. Using non-destructive testing on site at an early stage can enhance the precision of selective dismantling, particularly for attaining the desired product quality, thereby also reducing the time, energy, and cost involved. This allows the end-user to more effectively plan the selective dismantling of elements from existing structures and orchestrate the reusage scenario more precisely prior to dismantling.
By definition, non-destructive testing (NDT) makes it possible to verify the condition of an existing structure, to predict its durability, and to assess the quality of workmanship and potential for safe use. The most important advantage of NDT is the ability to establish parameters and a detailed physical description of the tested material at each stage of the structure’s existence. The parameters of wooden elements that can be determined using non-destructive methods are listed in Table 1 alongside the relevant methods [4], [5].
List of existing non-destructive methods for wood testing:
Modulus of elasticity | Ultrasound |
Density | Ultrasound, X-ray, Microwave, Resonance (NMR), Drilling, Electromagnetic methods |
Moisture | X-ray, Microwave, Resonance (NMR), Electromagnetic methods |
Layer thickness measurement | Optical, Electromagnetic methods |
Inhomogeneity | Ultrasound, Acoustic emission, X-ray, Microwave, Resonance (NMR), Electromagnetic methods, Thermography, Microwave, Visual inspection |
Cracks | Ultrasound, Acoustic emission, X-ray, Thermography, Visual inspection |
Decay | Ultrasound, X-ray, Thermography, Visual inspection |
Failure | Acoustic emission, Thermography |
Deformations | Optical laser, Acoustic emission, Visual inspection |
Stiffness | Ultrasound |
Conventional methods vs non-destructive methods: A case from Austria
The traditional methods for measuring wood strength properties, such as 3- or 4-point bending, are outdated in this era of recycling materials from existing buildings, because the processes themselves alter the properties of the material, rendering it unusable. According to findings from tests conducted by Salzburg UAS in collaboration with Karelia UAS and Jade UAS, the strength values of used wood measured with a non-destructive mobile testing method exhibit relatively high correlation with actual strength values.
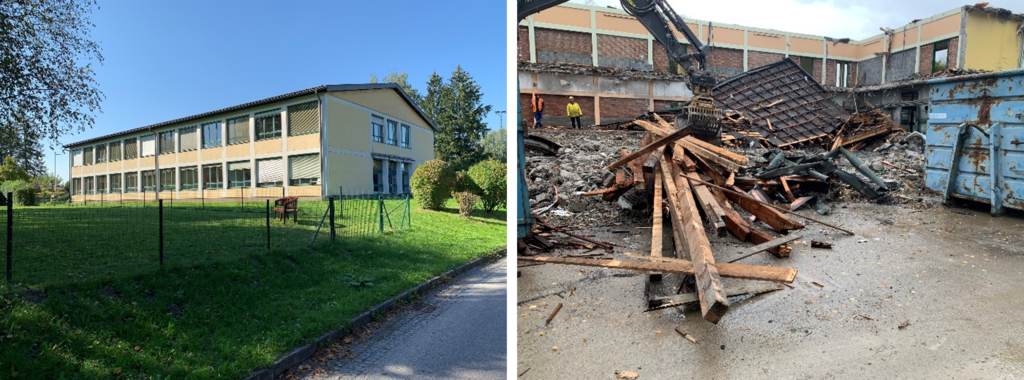
For this project, the wooden roof truss of a 50-year-old school building was dismantled, providing the research group with spruce beams that measured 14cm x 10cm in cross section with a length of approximately 4 meters. The density and the moisture content of each sample was determined, and visual grading was conducted. Subsequently, the mechanical properties of the wood were investigated using the time-of-flight method (TOF), a mobile and non-destructive testing method that measures the propagation speed of a sound impulse sent through the wooden beam, in a longitudinal direction, from a transmitter to a receiver. This sound propagation speed is measured with a microsecond timer device and used in combination with the density of the wood to calculate the bending stiffness. In order to confirm the accuracy of this method, the same beams were examined using the 4-point bending test according to the current standard.
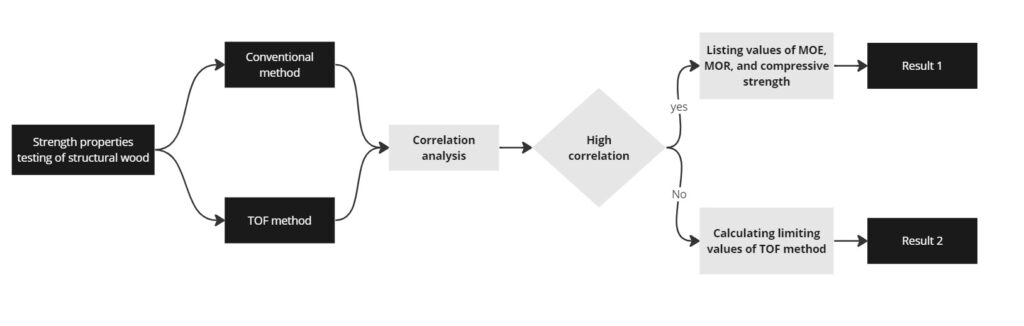
Figure shows the method adapted for comparison of the results from MOE static and MOE dynamic testing. When evaluating ToF results, it is important to remember that defining the strength of wood by means of the ToF method also necessitates determining the wood’s moisture content and raw density. Moisture content measurement is quite straightforward and non-destructive, but for raw density the options are rough estimation (e.g., based on year ring width) or, alternatively, accurate measurements of extracted samples (e.g., by core drilling). In the latter case, the method ceases to be fully non-destructive. Moreover, regardless of the adopted method, the results (calculated time of flight) should be compared or verified against situations where the tested element rests on a support or supports additional elements generating loads.
The results show that the correlation of the strength values between the TOF-method and the 4-point bending test is significant. With a coefficient of determination of 0.74, the values of the mobile testing method correspond to a relatively high degree with the actual strength values. Further tests to investigate parameters potentially influencing the result, including moisture content, wood species, and wood characteristics such as cracks and knots, will need to be conducted to improve the accuracy of the TOF-method. The aim of this research is to provide wood industry professionals with the means to determine the exact mechanical properties of used wood on site with this mobile and non-destructive testing method.
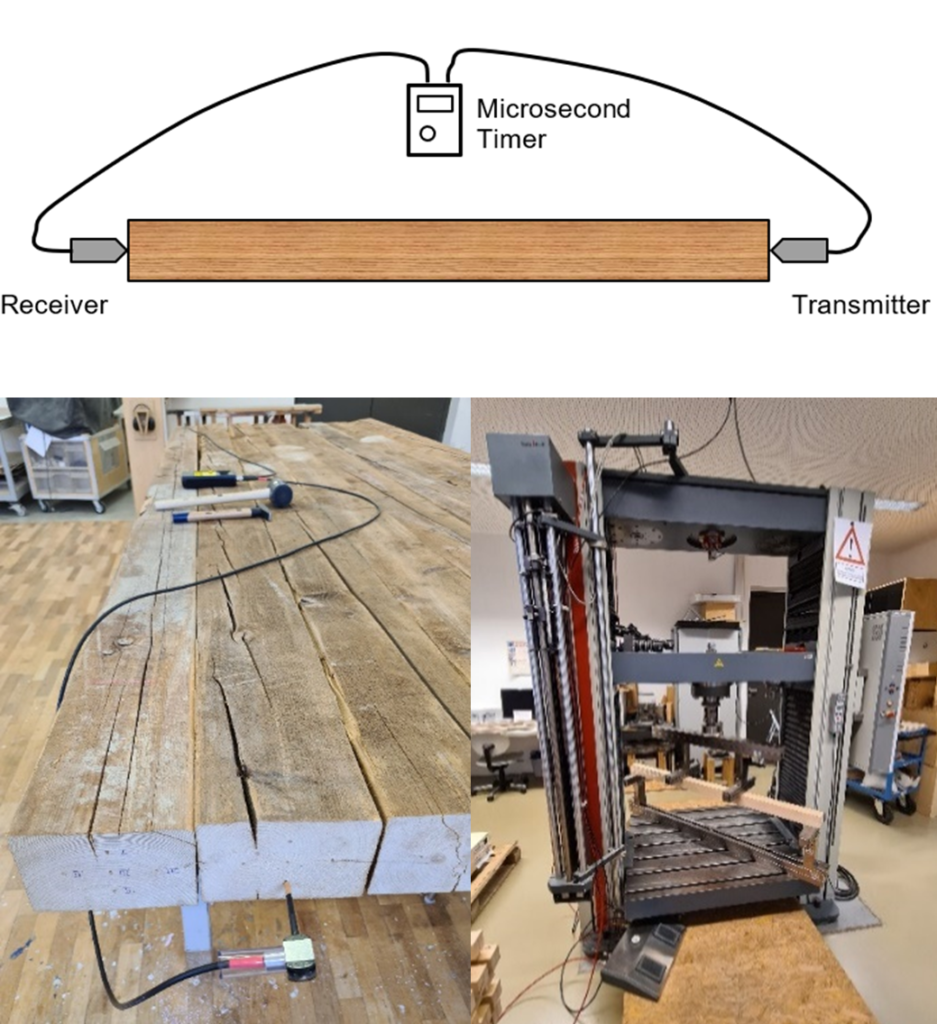
Correlation between testing methods
Figure shows the results of a 4-point bending test (MOE sta.) and those of a time-of-flight method (MOE dyn. direct, MOE dyn. indirect). Dynamic MOE values (direct measurement) of whole beam samples amount to a mean value of 12.829 N/mm², whereas for the indirect measurement method a mean value of 12.487 N/mm² was determined. A mean value of 15.367 n/mm² was determined for clear samples (direct measurement). On average, dynamic MOE values of whole beam samples were 16.52% lower than those of clear samples. The lower dynamic MOE values for whole beam samples can be attributed to the shorter sample length and the absence of wood defects in the clear samples.
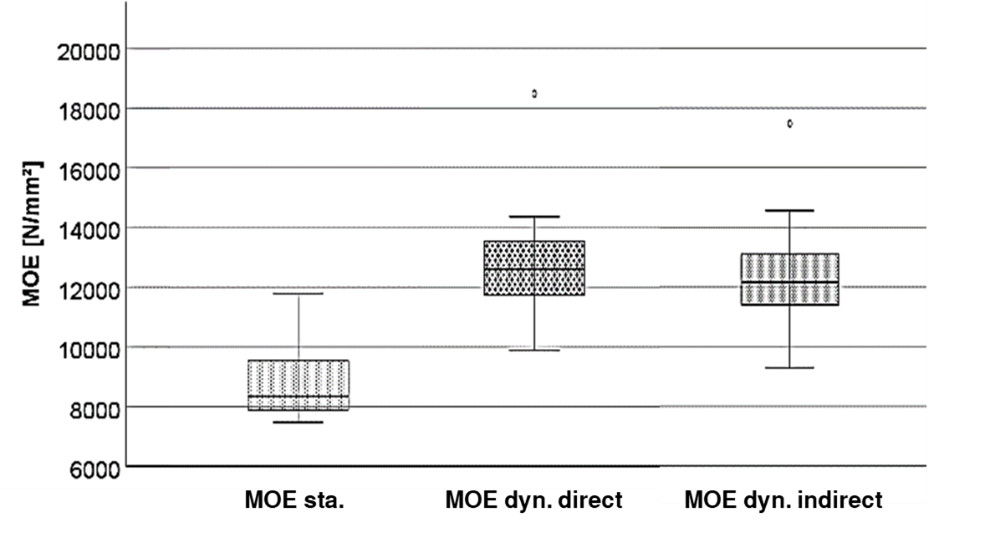
To attest to the accuracy of the investigated time-of-flight (TOF) testing method, the results of the static and dynamic MOEs are presented in Figure 8. The multiple correlation coefficient (R) was calculated for the correlation between dynamic MOE (MOEdyn) and static MOE (MOEsta). Both test methods and moduli of elasticity were carried out and calculated on complete samples with a length of 3000mm (whole beam) and on small, flawless samples with a length of 360mm (clear sample).
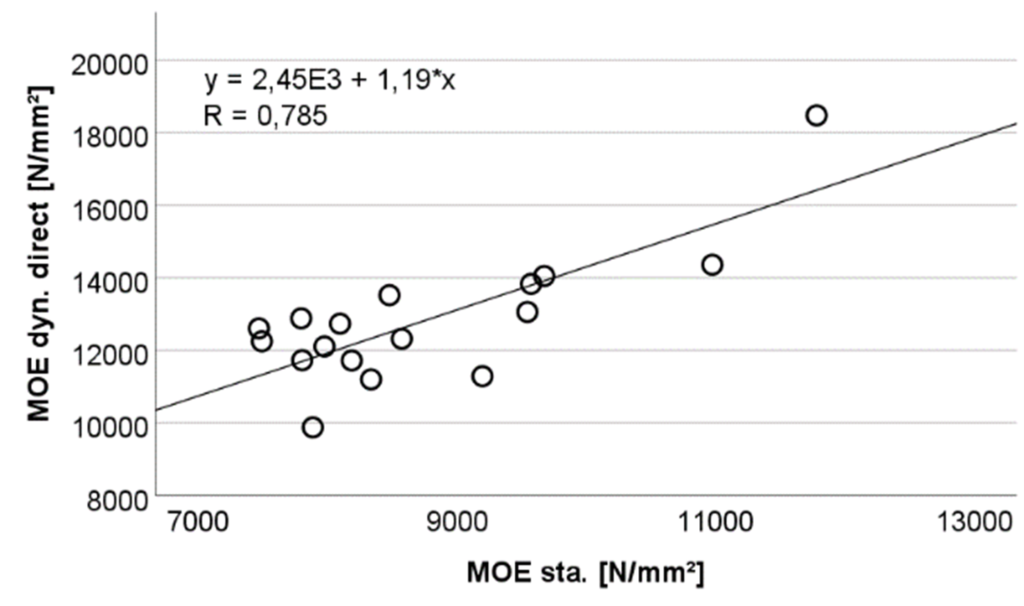
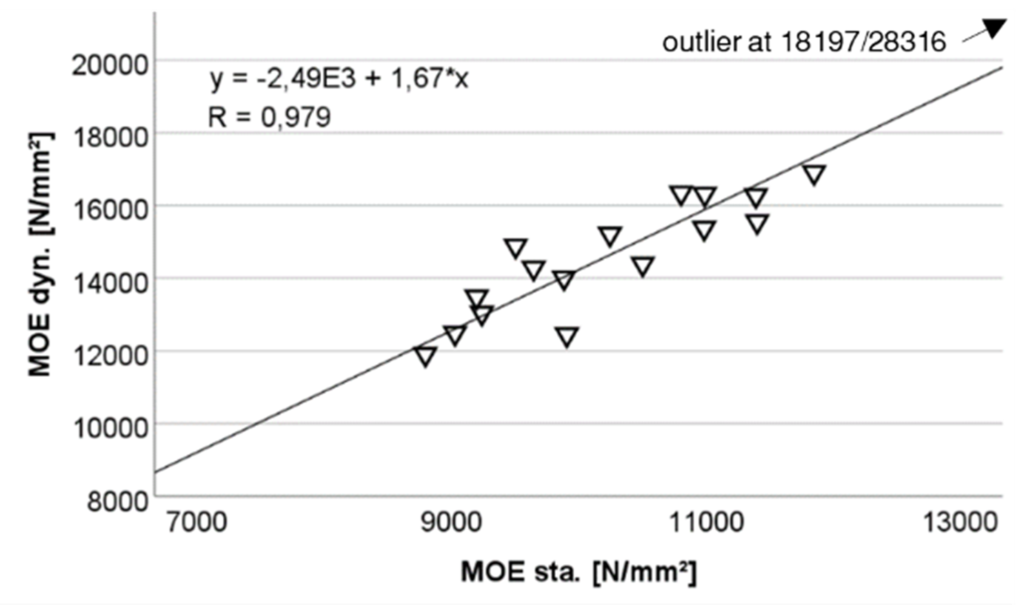
Correlation analysis between dynamic and static MOE for clear samples
The highest correlation between dynamic and static MOE was determined for clear samples, which with R = 0,979 indicates a strong linear correlation between the two applied methods. Sonderegger et al. (2007) determined a correlation of R = 0.938 for crack and knot free spruce samples. In comparison, the correlations for whole beam samples were R = 0.785 with the direct measurement method and R = 0.826 with the indirect, in other words 19.4% and 15.3% lower, respectively, than for clear samples. This lower correlation for whole beam samples can be explained by defects present in the whole beams, such as knots, cracks, and resin pockets, which lead to a lower static MOE but are not or only partly detected by the TOF method (Niemz, Mannes 2012).
Conclusion
The early-stage analysis of material intensity and strength property testing is crucial for optimising the reuse of construction materials in buildings, and especially to promote such reuse on a mass scale in cities. Non-destructive testing methods enable early-stage decision making for the selective dismantling and optimised scenario planning for the reuse of wood. The case study from Austria provides a better understanding of how non-destructive testing can help us sort the used wood reclaimed from a site with more accuracy. At the same time, it simplifies the process of early-stage identification of material strength properties, allowing for more efficient planning of the dismantling process. In addition, it allows us to predict the future usage purposes of reclaimed wood with more precision.
References
- YK:n ympäristöohjelma. (2022). (raportti). GLOBAL STATUS REPORT FOR BUILDINGS AND CONSTRUCTION. Noudettu 25. lokakuuta 2023. Saatavilla: https://www.unep.org/resources/publication/2022-global-status-report-buildings-and-construction.
- Nakajima, S., & Russel, M. (2014). Barriers for Deconstruction and Reuse/Recycling of Construction Materials. The International Council for Research and Innovation in Building and Construction.
- Michael H. Ramage, Henry Burridge, Marta Busse-Wicher, George Fereday, Thomas Reynolds, Darshil U. Shah, Guanglu Wu, Li Yu, Patrick Fleming, Danielle Densley-Tingley, Julian Allwood, Paul Dupree, P.F. Linden, Oren Scherman, The wood from the trees: The use of timber in construction, Renewable and Sustainable Energy Reviews, Volume 68, Part 1, 2017, Pages 333-359, ISSN 1364-0321, Saatavilla: https://doi.org/10.1016/j.rser.2016.09.107.
- Monika Zielińska and Magdalena Rucka 2021, Non-destructive Testing of Wooden Elements, IOP Conf. Series: Materials Science and Engineering. doi:10.1088/1757-899X/1203/3/032058. Saatavilla: https://iopscience.iop.org/article/10.1088/1757-899X/1203/3/032058/pdf#:~:text=These%20include%20ultrasound%20methods%2C%20impulse,waves%20through%20a%20structural%20element
- P. Niemz, D. Mannes, “Non-destructive testing of wood and wood-based materials,” Journal of Cultural Heritage, 13S, pp.26–34, 2012.