Wood City – the Flagship for Finnish Wood Construction
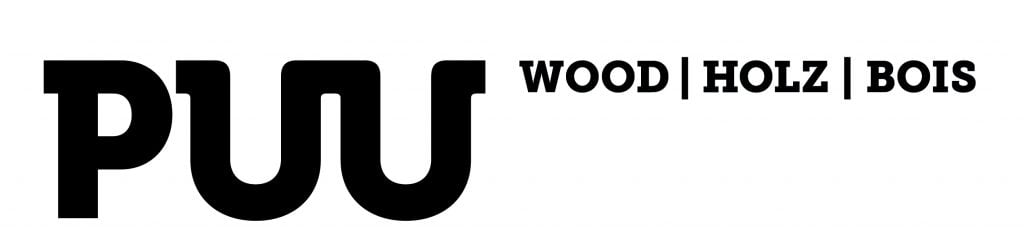
The article has been published in June 2021 in Wood magazine 1/2021.
Read the article in Finnish: Wood City – suomalaisen puurakentamisen lippulaiva
Text: Mia Heiskanen ja Heidi Tetteh, Photos: Tuomas Uusheimo
The result of collaboration by SRV and Stora Enso, Wood City is a series of wood buildings centrally located in the Jätkäsaari district of Helsinki. The project has drawn interest from around the world as a flagship of Finnish wood construction, and Wood City truly is a fine example of the versatile ways in which wood can be used in buildings. Wood City includes the new headquarters of Finnish gaming company Supercell, and their office is now the largest wood office building in Finland as measured by the amount of wood used.
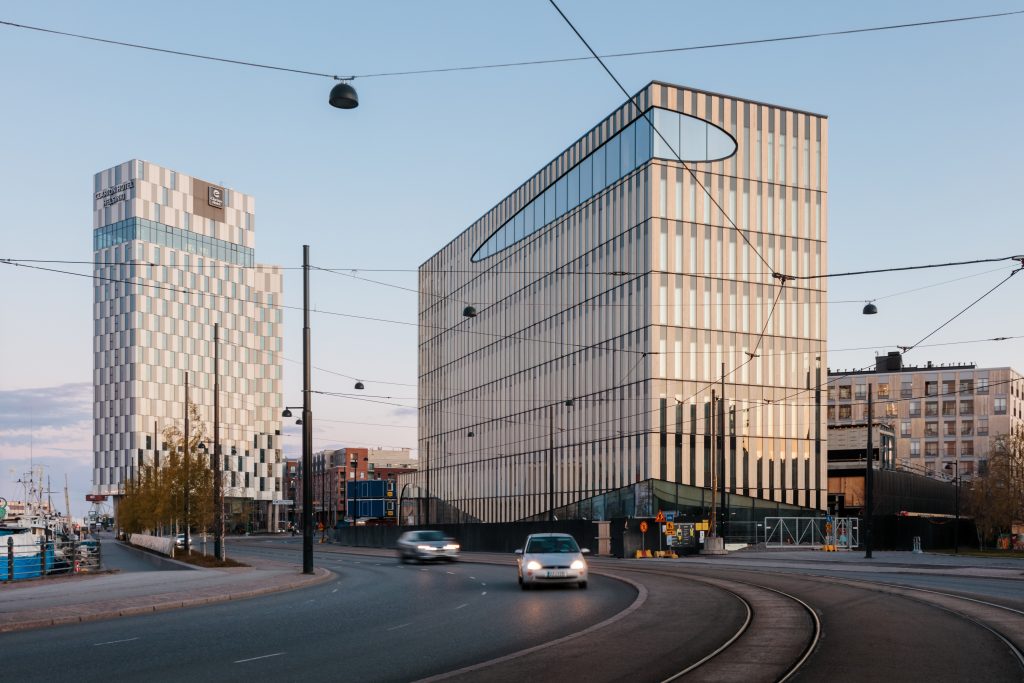
T wo residential apartment buildings (phase 1) and an office building (phase 2) have been completed in Wood City, with a hotel still planned to come (phase 3). All the buildings are eight storeys tall. The buildings in the complex will also share a three storey car park (part of phase 2).
The new building completed in Wood City includes an eight-storey wood office building and a three storey car park with 170 parking spaces. The office building serves as Supercell’s new headquarters. The ground floor, basement and stiffening vertical shafts are made with concrete. The 1st through to 7th floors are wood, with the load-bearing structures being LVL pillars, beams, and slabs. The facades have wood cladding. The laminated veneer lumber (LVL) is from Stora Enso’s facility in Varkaus, with the wood mostly coming from private forest owners in the surrounding region of Savo. The CLT came from a Stora Enso facility in Sweden, with the wood mainly coming from Stora Enso’s own forests in the nearby area.
Supercell’s headquarters is the largest wood office building in Finland as measured by the amount of wood used. This qualifies as an eco-action, as this amount of wood binds the CO2 equivalent of a year’s driving for 600 passenger cars.
Aiming to be the best work environment in the world
The gaming company Supercell Oy moved to the office building in Wood City with the aim of creating the world’s best work environment for its employees.
This rather ambitious goal was broken down into the following targets:
- First-class quality
- Superior surroundings
- Flexible configuration
The design solutions focused on creating superior surroundings. Examples include air conditioning, careful material choices, and first-class acoustics that include a sound masking system. The flexible space configuration takes user needs into account. The resulting solution also facilitates the reconfiguration of office spaces for future needs.
An open office culture lies at the core
From the very beginning, the project sought to engage employees and to promote transparency and teamwork. The aim was to consciously facilitate the Supercell mindset where teams openly share knowledge and lessons with each other. The project team included people from the SRV project and site management group, project architect from AOA as well as representatives from Supercell and the HTJ construction consulting services hired by Supercell. The team wanted to do things right and according to a properly managed plan, but they also wanted to challenge the traditional ways of doing things.
Although this was a turnkey project, the approach included collaborative methods. The site is testimony to the fact that collaboration does not always require alliances. As the project progressed to the construction phase, the client was very much part of the process. The project sought ways to challenge traditional ways of working and to make the client’s corporate culture part of the construction site processes. This turned out to be an important operating model because a lot of changes and even completely new systems came up during construction. Changes in the team space layouts in December 2018 were the single biggest change. This totally transformed all the interior structures and the systems the users wanted, all while the concrete framework was already being poured.
The subcontractors were brought together in Last Planner sessions twice a week, which allowed them to coordinate their work for the upcoming phases. Last Planner sessions were an important tool for managing changes during construction. They allow everyone to react quickly to changes and to share information effectively with all the contractors. The subcontractors showed an excellent level of participation and were eager to commit to the shared goals of the project.
Quality walks and gates
One of the important keys to success was the level of quality Supercell wanted. The project team knew from the start that this site would require more scale models on site than usual. To support the design work and to test the user experience, a 1:1 scale model of a team space was created for the project. This made it possible to test different technical, structural and surface material options.
The project team recognized that the best way to reach superior quality standards was to get everyone to commit themselves to the goal and to work together to get the best possible outcome. Strong collaboration was key. Contractor and/or building component specific quality walks and gates were used to encourage quality workmanship and to highlight the importance of the required quality. On quality walks, the project team inspected building components or end results on-site together with suppliers/subcontractors. It was beneficial to have Supercell available on-site as it meant workers were able to receive feedback from the actual end user.
A stocking-foot construction site office and a grill for the workers
From the start, the concept of a good working environment was extended to include everyone at the construction site. While the site office was a traditional office trailer often seen on construction sites, the interior was made more pleasant with light-coloured paint, some greenery, a free coffee machine, and adjustable desks for all who wanted them. Wall-to-wall carpeting was installed in the office, creating SRV’s first-ever stocking-foot site office.
The shared goal was to make the working conditions so pleasant that trained workers would not want to switch to another site. To further this goal, a management team for workers with one representative (not a foreman) from each subcontractor was created at the beginning of the project. This team met for lunch with SRV and Supercell project management once a month. Over lunch, the team discussed working conditions and development areas in a free-form manner. The intention was also to inspire the participants to challenge traditional operating models. This model provided valuable, “unfiltered” information on site conditions, which was then used to improve working practices. A grill area was also set up on the site, which made workers feel more comfortable and helped maintain the social distancing required in the Corona era. Workers also had common lunch breaks where Supercall offered lunch for the entire site. This made it easy to share news and gave people a sense of team spirit.
Zero accidents
Occupational safety received special attention right from the project’s planning stage. As there was very little room to maneuver on the site, careful planning was required to ensure safety not only on the site itself but also for other operators nearby. The accident rate for SRV on the site was zero. The average for the entire site was 17.88, which can be considered to be a good result considering the 475 thousand hours worked. The site particularly excelled in making safety observations. A total of 1,278 observations were made in 2019, which is the highest across all SRV construction sites. Safety gates were conducted once a week by SRV’s management.
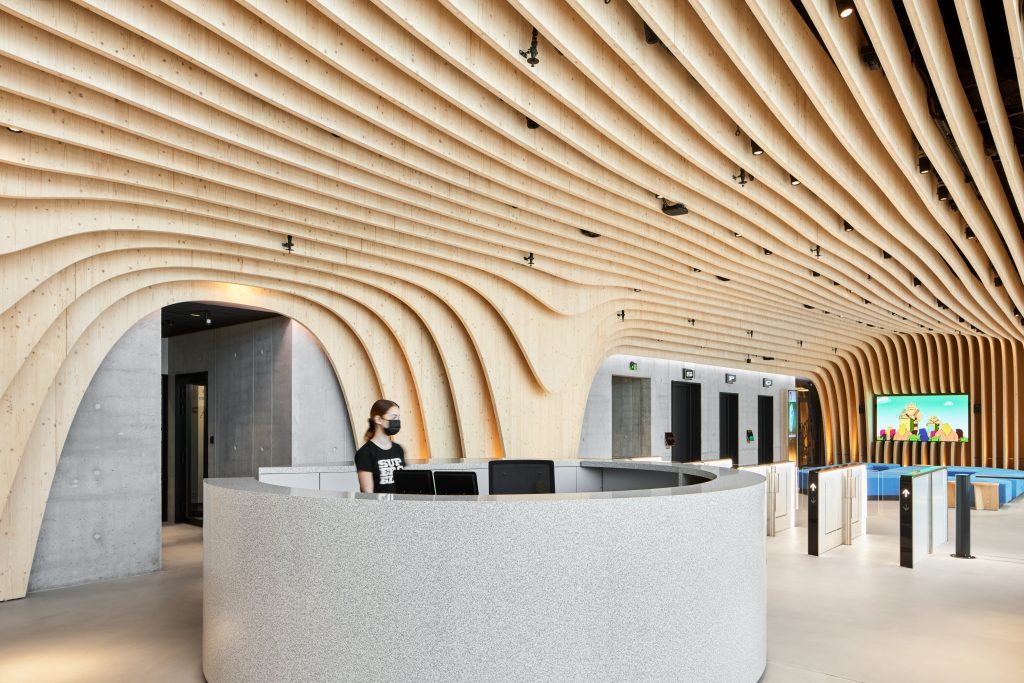
Successful moisture management
For moisture management, the project team worked with leading experts to develop a detailed moisture management plan for the construction phase. This plan was followed meticulously. The core principle of moisture management is that concrete and wood framework structures can be exposed to rain or humidity in a controlled manner when favourable conditions are provided for these structures to dry off after they get wet. The structures then begin to dry according to their natural moisture retention behaviour. The intermediate floor elements were sealed, the edges were dammed up, and rainwater was directed down from the top vault via rainwater channels to concrete stairwells. When the frame was put up, critical wood frame materials (façade elements, load-bearing LVL elements) were stored with their moisture-sensitive parts protected. Façade installation work overlapped with the installation of the frames. In other words, a façade was installed for each floor as soon as the floor above it was completed.
The moisture management plan was followed closely. As part of their initial training, every employee on site went through a separate moisture management session to ensure they understood the basics and importance of moisture management. Separate moisture management rounds were conducted weekly, and the results were reported directly to the Helsinki Building Inspectorate. Handling moisture management was of paramount importance, and its success was critical to the entire project. Extensive advance planning and collaboration were key. The Building Inspectorate’s feedback has been excellent on this issue. As an indication of the exceptionally good co-operation with the Building Inspectorate, the construction site received the 2020 Rakentamisen Ruusu award.
- Location: Jätkäsaari, Helsinki
- Purpose: office building
- Developer/client: Supercell Oy
- Architectural and main design: Anttinen Oiva Arkkitehdit Oy / Vesa Oiva, Selina Anttinen, Matti Huhtamies, Teemu Halme
- Structural design: Sweco Rakennetekniikka Oy / Antti Vilén, Maija Tiainen
- Foundation design: Ramboll Oy/Petri Tyynelä
- HVAC design: Climaconsult Oy / Juha Pentikäinen, Harry Gullberg
- Electrical design: Sweco Talotekniikka Oy / Jyrki Kokko
- Sprinkler system design: Festec Oy /Jouni Ryyppö
- Fire safety design: KK-Palokonsultti Oy / Esko Mikkola
- Main contractor: SRV Rakennus Oy
- Construction consult: HTJ Oy
- Supplier of wood material: Stora Enso
- Supplier and assembly of CLT elements: Puurakentajat Group Oy
- Manufacturing of CLT elements: Timberpoint Oy
- Construction schedule: 6/2018 – 12/2020 (includes work and installation by Supercell)
- Total area: 19 150 brm2 of which the office building is 13 650 brm²; parking garage 5 500 brm2
- Volume: 61 200 rkm³ 8 floors + basement, 7 lifts
Wood City will be presented at the Wood Day on November 4, 2021, register and hear more: www.puupaiva.com
- Read the whole Wood magazine 1/2021.
- The next magazine will be published in October 2021. Subscribe it now.
- Articles selected by Wood Magazine advertisers are published as e-articles in addition to the print magazine.
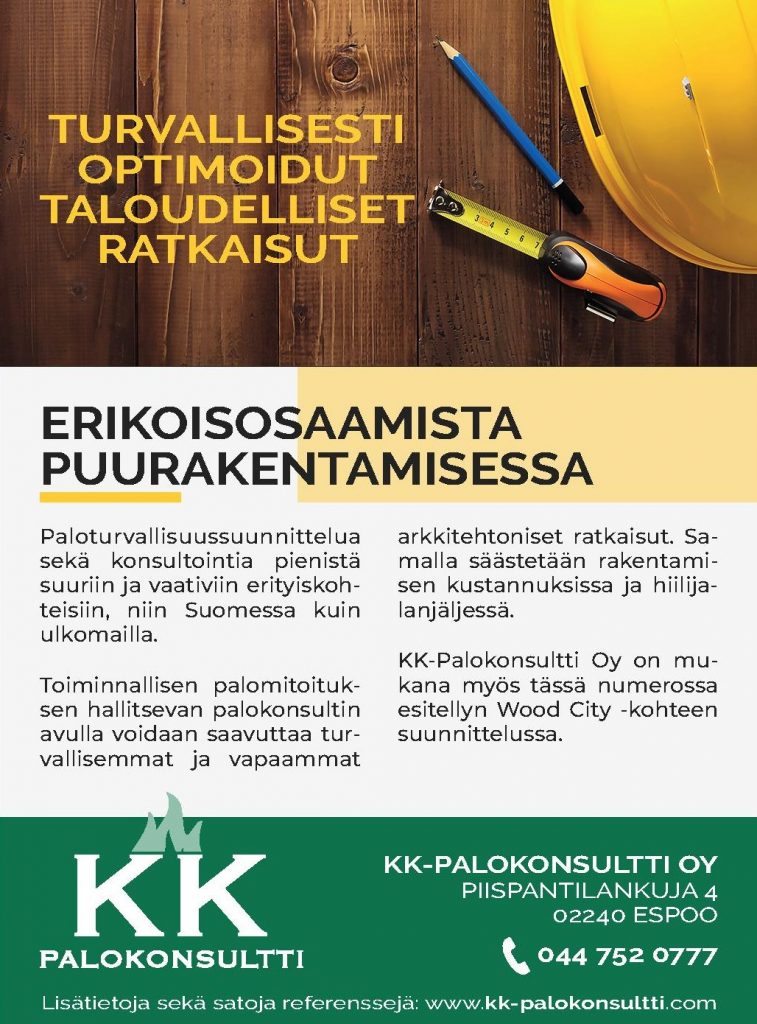
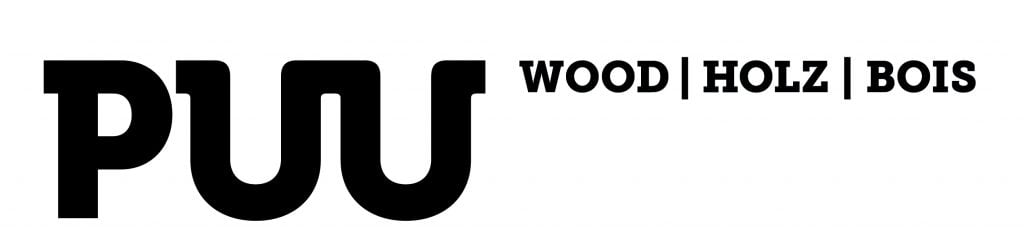