Wood rises to the surface

A facade is like a building’s calling card as it entices people to step inside to take a better look. The materials, colours and shapes define a building’s character. Facades need to withstand time but also represent their own era.
Text: Inkariina Sipiläinen
Read the article in Finnish: Puuta pintaan
A wooden façade that is well-designed and executed – and properly maintained – can last for decades upon decades. Finland even has numerous examples of wood facade buildings that are more than 100 years old.
When choosing facade materials, the prevailing weather conditions must be taken into account. For example, a sunny marine environment will place a facade under considerable weather stress. The inherent durability of different materials varies depending on the type of wood used, but the long-term durability of some materials can be improved with surface treatment agents.
The demand for wood products has increased during the corona pandemic, which has occasionally led to a shortage of cladding materials. Juho Kallonen, CEO of the lumber company Lauta Oy, says that demand was high all last year. Materials sourced in Finland have been somewhat more available than imported products.
Kallonen says that the choice of cladding material is often a balance between a product’s appearance, environmental effects, and price. Cladding material prices vary significantly, but the differences level out when life cycle costs are considered.
To treat or not to treat?
There are several different types of wooden cladding available. Wood can be modified with a variety of methods, it can be surface treated, or used as is. In addition to their aesthetic effects, surface treatments also protect wood materials.
Industrial surface treatments guarantee controlled and optimal humidity, temperature, and cleanliness. Industrially painted cladding boards speed up construction on site and protect against the weather during installation. Primer should be applied as soon as possible after planing. Alternatively, cladding products that are partially or completely pre-painted are also available. These products are installed using concealed mountings. Olli Prättälä, Sales Director of Siparila Oy, says that the demand for industrially pre-painted products is constantly growing.
Facade fire protection
When building apartment or public buildings that are more than 2-storeys tall, wood needs to be fire protected. In multi-storey buildings, the ground floor and exit route surfaces must have class B-s2, d0 fire-protection. The recommendation is to apply fire protection treatments in industrially standardised conditions.
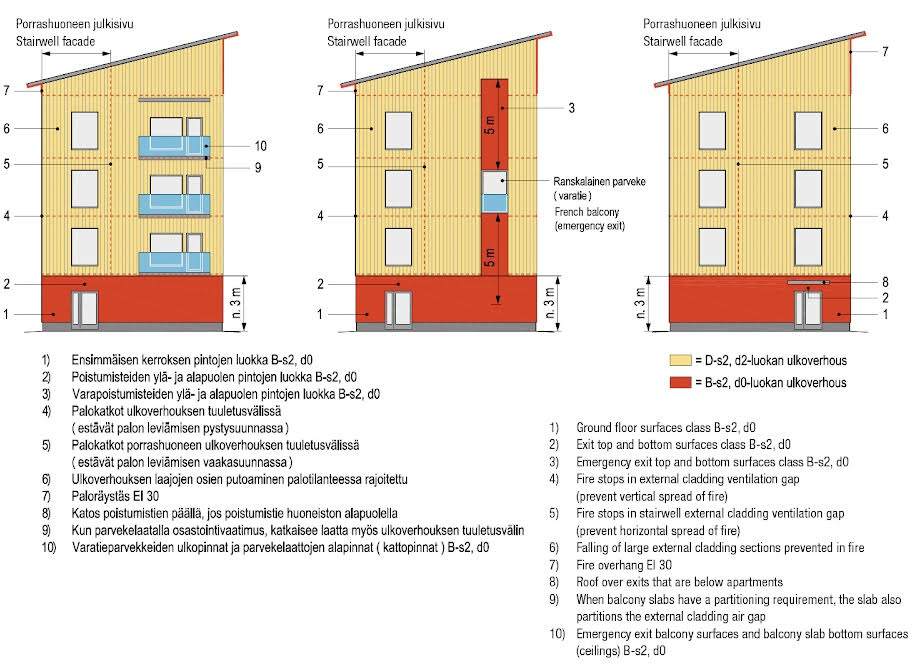
For more information, see: Paloturvallinen puutalo (Fire Safety in Timber Buildings).
Accoya
Accoya® is a brand for environmentally friendly, non-toxic acetylated wood. In the acetylation process, the wood is impregnated with a concentrated vinegar solution, which changes the cell structure permanently. The wood becomes very moisture resistant and retains its shape well. Accoya® needs no separate surface treatment. Rather, it has an up to 50-year warranty for untreated above-ground structures.
According to Petteri Huomo from Novenberg Oy, Accoya’s strengths are its long life cycle, maintenance-free nature, and environmental sustainability. The product is made from radiata pine, which is obtained from Spain and New Zealand, among other places. There is only one processing plant in Europe, which has led to occasional availability challenges.
Novenberg’s long-term goal is to develop the Accoya treatment to suit northern pine as well. This would bring a Finnish product version to market. Due to their long service life and ability to retain their shape, Accoya products are constantly increasing in popularity. Huomo says that the feedback has generally been very good.
Accoya facades do not splinter. Left untreated, the wood turns grey in a few years depending on the location of the site, the surrounding vegetation, and other environmental factors.
For more information, see: www.novenberg.fi
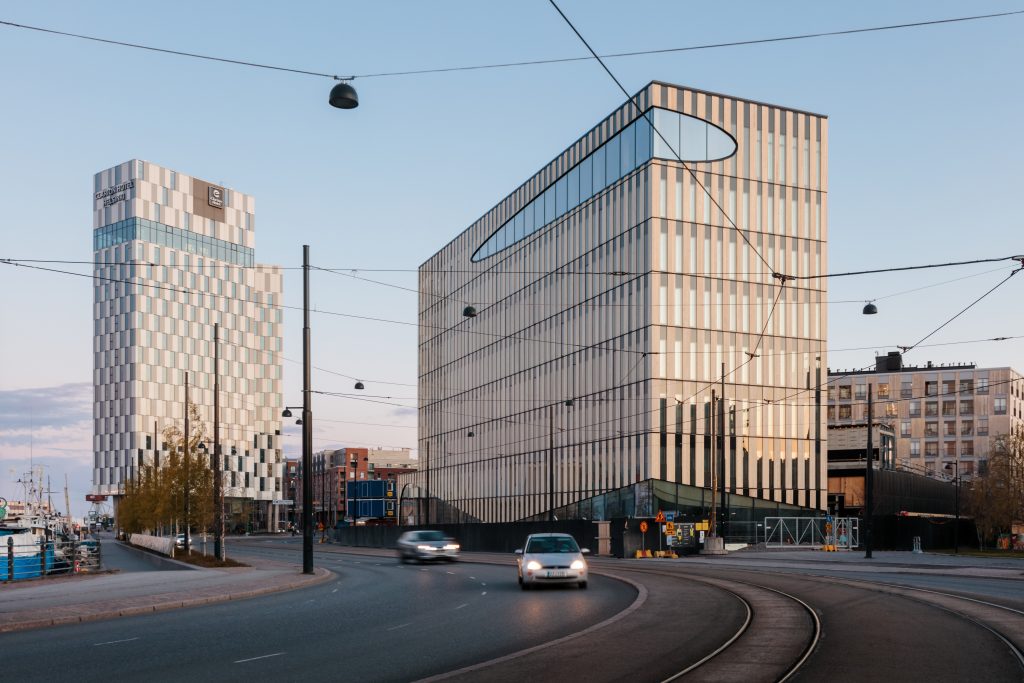
Wood City
Located in Jätkäsaari, Helsinki, the Wood City complex is the result of collaboration between SRV and Stora Enso. Wood City includes apartment buildings, an office building, a hotel, and a car park. These modern buildings are located by the sea, which means they are subject to extremely variable weather conditions. The facade’s durability and maintenance-free nature heavily influenced the choice of material. Part of the facade has been treated to fire class B-s1, d0 with Burnblock fire protection agent. Wood City’s Accoya facades have an 80-year maintenance-free warranty. The Wood City was designed by Anttinen Oiva Architects.
Larch
The natural properties of larch make it a very durable building material. Larch contains nature’s preservatives such as resin, rosins, and minerals. It stays maintenance free for several decades when installed off-ground. Cladding panels made from larch do not need surface treatment, as larch withstands the stress of UV radiation and moisture on its own. The thicker the material used for cladding, the better it lasts over time.
Panels made from larch give facades a natural look. Larch cladding turns grey over the years – the stress of weathering affects how quickly this happens. In the beginning, the facade surface may have an uneven tone. Larch can be treated with ferrous sulphate to accelerate the greying process, if desired. Applying a translucent treatment is not recommended because the maintenance interval for translucently treated larch is double that of Finnish spruce.
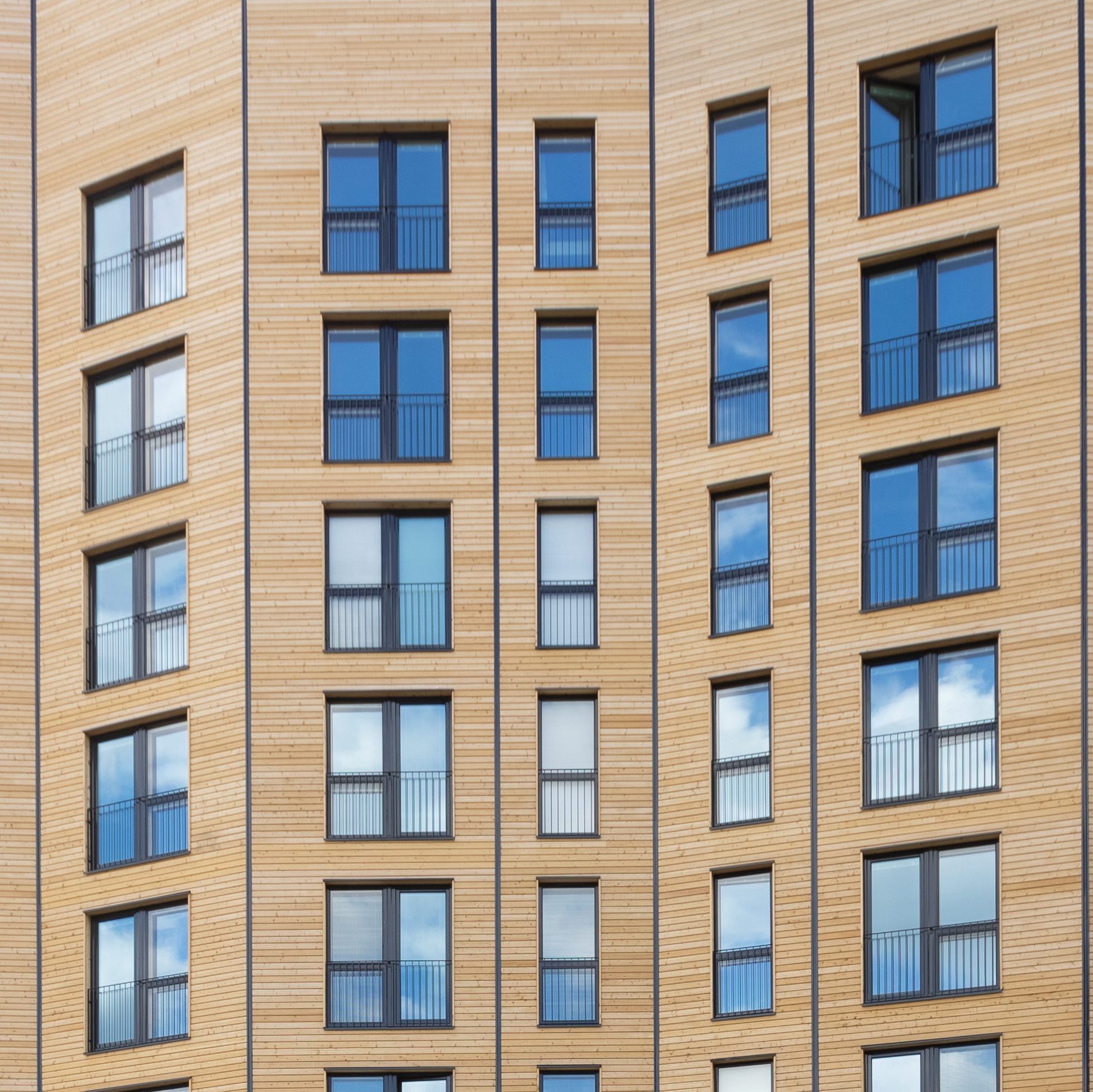
TOAS Kauppi
Kauppi’s facade has a unique accordionlike look, with all the apartments having a slightly different view. Untreated planed larch was chosen for the facade cladding. The aim was to use the horizontal cladding to blend over the horizontal seams of the facade’s CLT elements. As a deviation from traditional wooden construction, the vertical seams have novel detailing TOAS Kauppi was designed by BST-Arkkitehdit Oy.
PLATTA facade panels
PLATTA facade panels are made from cross-laminated, 3-layer spruce glulam sheets. This makes the panels easy to process but light to use. The panels are available in three different lengths. They are all pre-painted, which means they do not need to be surface treated on site after installation. The maintenance interval is the same as for spruce cladding in general, meaning 10–20 years depending on the site.
PLATTA facades also present a completely nail-free appearance. The PLATTA panel solution makes it possible to use different colours and widths on the same wall surface. Facades can combine light-colours and different-widths to form a pattern, for example. The panels speed up the construction process and can be installed either on site or at the element factory. For more information, see: www.siparila.fi

HOAS Tuuliniitty
Tuulinitty uses Siparila’s 20 mm thick, prepainted PLATTA facade panels for its facades, which were installed with concealed fastenings. The panels have been treated with Tikkurila’s Ultra Pro 30, which protects from weather, moisture, UV radiation, and dirt. The light parts of the facade are PLATTA panels, while the dark parts are lamellae that were also painted with Tikkurila products. HOAS Tuuliniity’s chief designer was Arkkitehtitoimisto Jukka Turtiainen Oy.
Thermally modified wood
The actual breakthrough leading to thermal modification took place in Finland in 1993. ThermoWood®, manufactured using this thermal modification method developed in Finland, has since been standardised and producers are subject to audits via a quality control system.
Jukka Ala-Viikari, CEO of Lämpöpuuyhdistys ry, notes that thermal wood‘s ability to retain its dimensions and shapes means that structures and fastenings do not begin to leak over time. Thermal wood’s lack of resin is helpful during surface treatment.
Lunawood Oy ’s Maija Masalin emphasizes the responsibility aspect: no chemicals are used in production. Instead, thermal modification is based on changing wood’s properties using heat and water vapor. At the moment, natural and black shades of thermal wood are the most popular in facades. Thermal wood may not need any surface treatment during its life cycle if the cladding’s natural greying is acceptable.
For more information, see: www.thermowood.fi; www.lunawood.com.

Aurum
Completed in spring 2021, Aurum houses a significant number of laboratory facilities shared by the University of Turku and Åbo Akademi University. Aihio Arkkitehdit Oy’s Piia Viitanen was the building’s main designer. She notes that there the design intentionally centered on making the building pleasant – almost as a counterweight to the sterile laboratories. One thing was clear: the facade was to be built with Finnish wood. In addition to the sustainability aspects of local sourcing, the material needed to be as durable as possible. The choice was made to go with Finnish thermally modified wood. Aurum’s impressive main entrance is clad with thermally modified wood, and the same material continues inside the lobby. Viitanen says that the goal was for the building to be inviting and to have a stylistic unity. The building has received very positive feedback from its users.
Charred surfaces
Wood has been charred since the dawn of time to improve its durability. Charring the surface creates a natural protective layer that improves the wood’s resistance to rot and moisture in particular. Also known as the Shou Sugi Ban method, charring has its roots in Japan. Charring can be used with all kinds of wood. The surface texture and the depth and speed of the charring depend on the wood species.
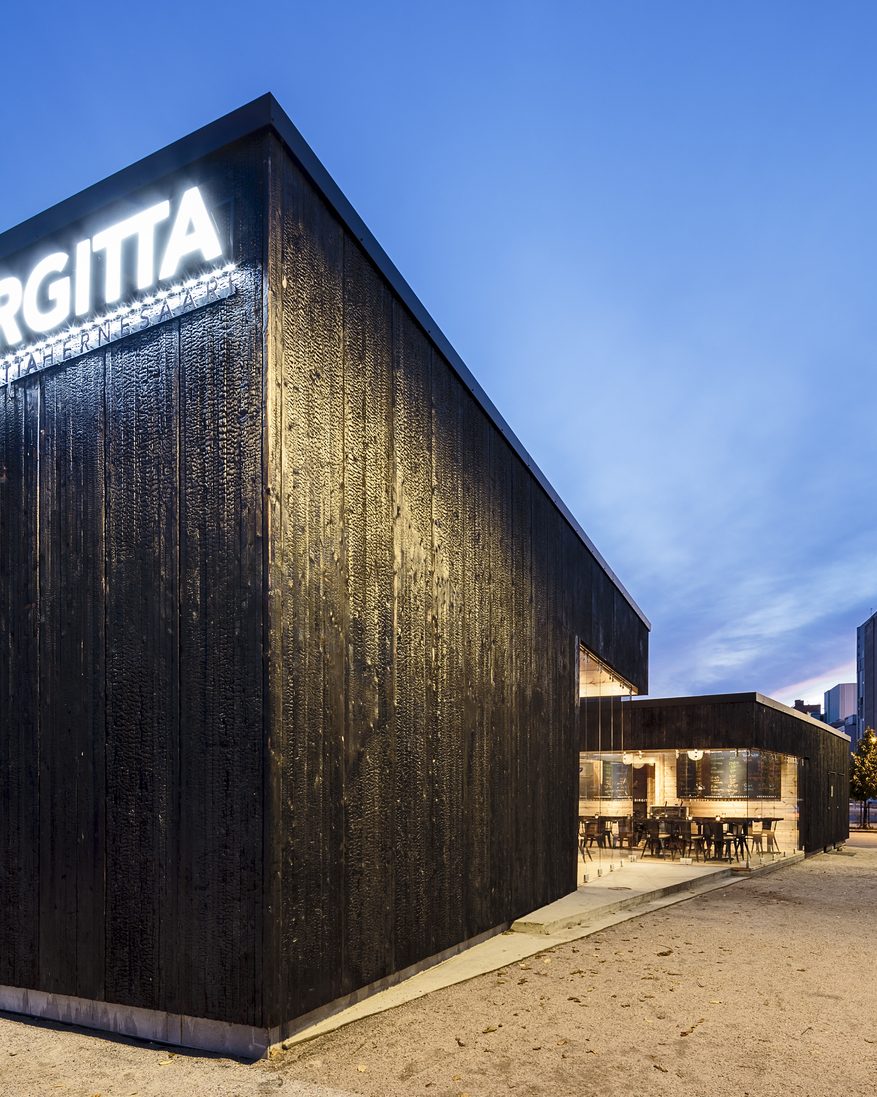
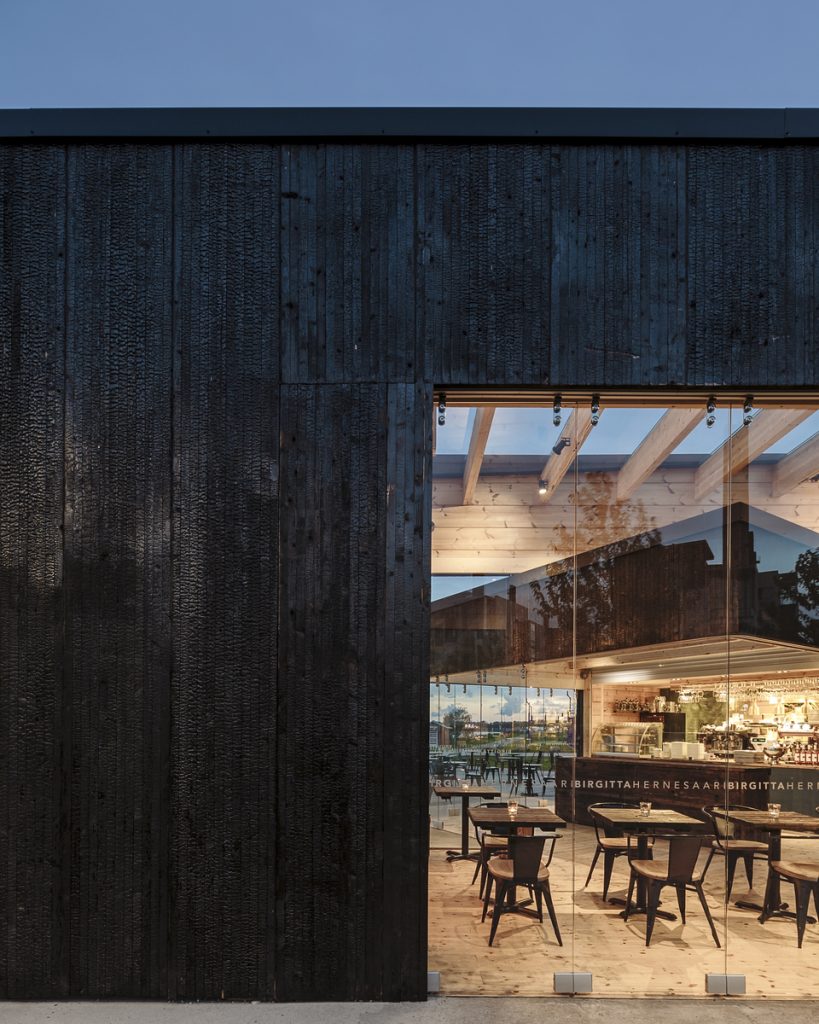
Cafe Birgitta
Located in Hernesaari, Helsinki, Cafe Birgitta has bright interiors that serve as a great contrast to the building’s dark exterior cladding. The aim was to make the café architecturally unique while blending in well with the surrounding seascape. The exterior walls of this log building are made from 50×50 mm laminated wood with a surface that was charred on site. The project was designed by Talli Oy, an architecture and design company, and it won the Log Building of the Year award in 2014.
Finnish spruce cladding
Of the wooden cladding materials discussed above, spruce cladding panels are the most popular and cheapest option. However, these panels have the shortest maintenance interval of the cited options, and this is reflected in its life cycle costs.
Following basic requirements, the maintenance interval for spruce cladding is 10–15 years. Proper and timely maintenance painting is an absolute necessity for the long-term durability of wood cladding. A number of profiles are available, and surface treatment options are abundant.

Table 1. Properties of different wooden cladding products.
Material | Appearance | Maintenance | Features |
Accoya | Turns grey in a few years May look mottled before surface evens out in the end | 50 year durability guarantee Facade cleaning and brushing as necessary | Maintenance free, durable, rot-proof |
Larch | Heartwood stands out from the lighter surface wood Turns grey over time | Properly installed, it easily lasts 50 years; wash as necessary No need for surface treatment | The wood’s inherent properties improve the biological durability |
PLATTA facade panels | CLT panel surface, completely pretreated product with concealed mounting Only available with opaque treatment Three different sizes available | Maintenance interval 10–20 years | Quick to install, light product, produced locally in Finland, good weather resistance |
Thermally modified wood | Initially dark, but turns grey in a few years | Can be used without surface treatment Surface-treated thermal wood requires maintenance on site, longer maintenance interval thanks to lack of resin | Produced locally in Finland, retains its shape well, resin free, good biological durability |
Charred surfaces | Distinctive appearance Stains without surface treatment | Applying oil every 5-15 years improves long-term durability and appearance | Good rot and moisture resistance |
Spruce cladding | Traditional wood cladding material Available with primer, or partially or completely industrially pre-painted | Maintenance interval 10–20 years | Flexible, produced locally in Finland, affordable |
Prerequisites for functional and long-lasting exterior cladding:
- Use a sufficiently thick cladding board, the recommended thickness is 28 mm
- Use cladding board industrially treated with primer
- The board should be made from heartwood lumber
- Install and surface treat cladding board that is sufficiently dry (moisture
- Install the boards with the heartwood side facing out if not using boards with industrial surface treatments
- Avoid seams and exposing the unprotected ends of cladding boards to weather
- Use end-matched tongue and groove and finger-jointed cladding boards
- Leave an open ventilation gap of about 22-25 mm from the bottom up behind the cladding
- Wood cladding must be able to dry freely after getting wet, and rainwater cannot be allowed to be absorbed into the structures (sloping surfaces, drip edges, protective coverings)
- Provide structural protection for the cladding such as eaves and sufficient distance from the ground to the lower edge of the cladding (recommended > 500 mm)
- Install, fasten, and surface treat properly
- Create a drip edge at the bottom of the cladding
- Functioning window sills and mouldings/lining boards for windows
- Properly constructed gutters and downspouts
- Eaves at least 300 mm wide, preferably 600 mm
- Inspect, repair and perform maintenance on cladding at sufficient intervals
The article has been published in October 2021 in Wood magazine 2/2021.
- Read the whole Wood magazine 2/2021.
- The next magazine will be published in the spring of 2022. Subscribe it now.
- Articles selected by Wood Magazine advertisers are published as e-articles in addition to the print magazine.
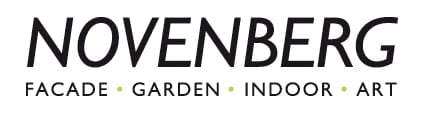
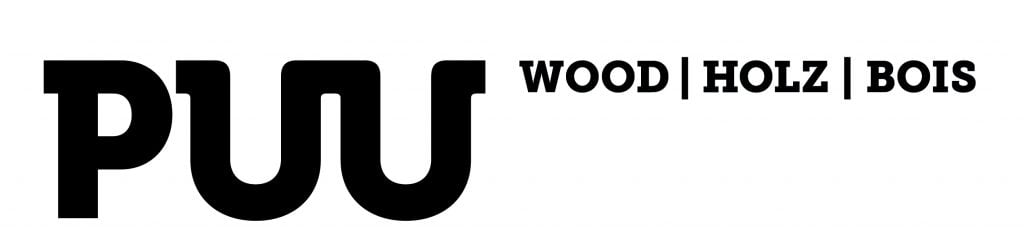