Contracting models for wood construction
When selecting a contracting model for a construction project, it is important to consider how the design and construction will be interacting in the project. The main questions are who is responsible for creating the design and will the project be done sequentially (design, then construction) or in parallel (design and construction overlap).
The contracting model determines how the clients, developers, designers, construction company, and other suppliers in a construction project divide up the work amongst themselves. This includes the duties and obligations of the parties, their relationships, how they contribute, and the principles by which they share risks and benefits.
There are several different systems and construction models in wood construction, which is why certain client decisions must be made earlier than usual. All forms of contract are possible, but the client must know the market’s supply well.
Text: Ympäristöministeriö/Puuinfo, Hankintaopas, lähde: Vison Oy
Read the article in Finnish here.
Rakennushankkeen läpiviennin periaate erilaisin toteutusmuodoin sekä osapuolia integroiva vaiheistus (musta rajaus)
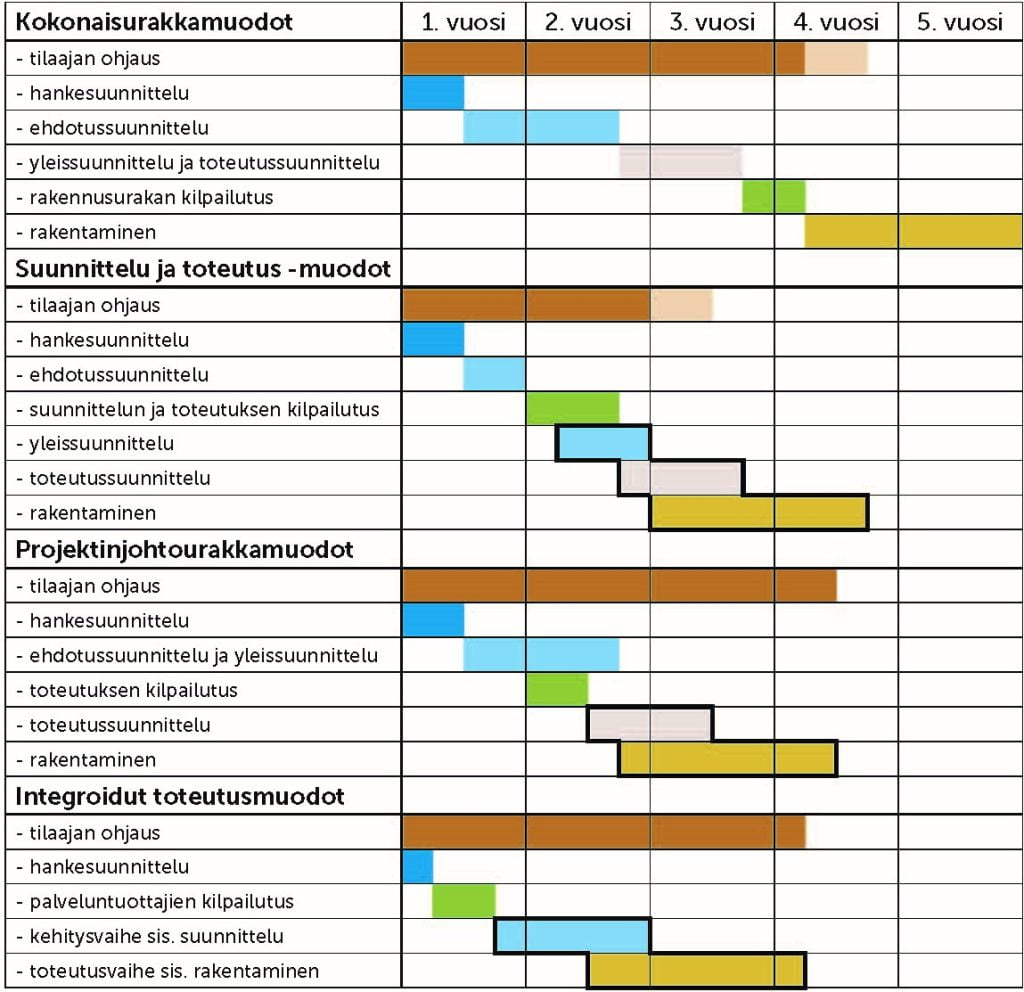
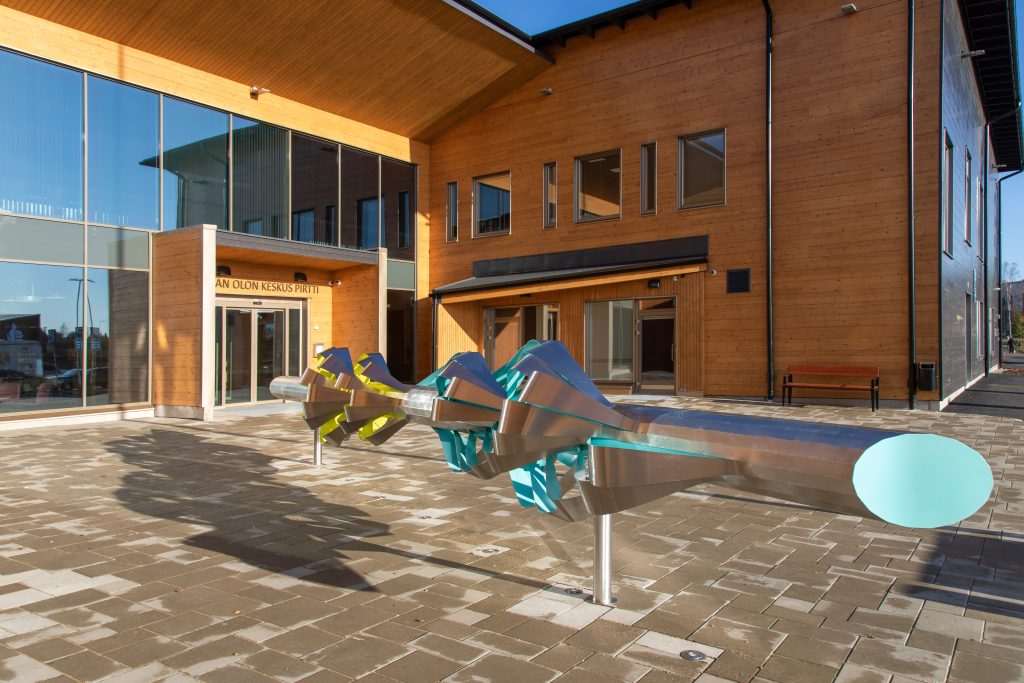
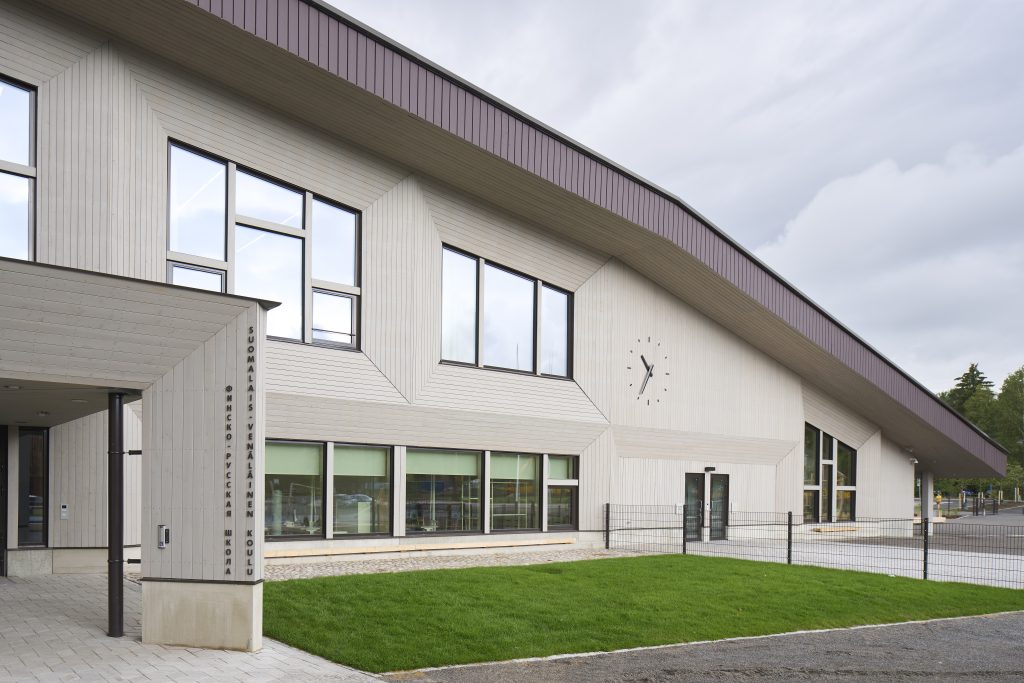
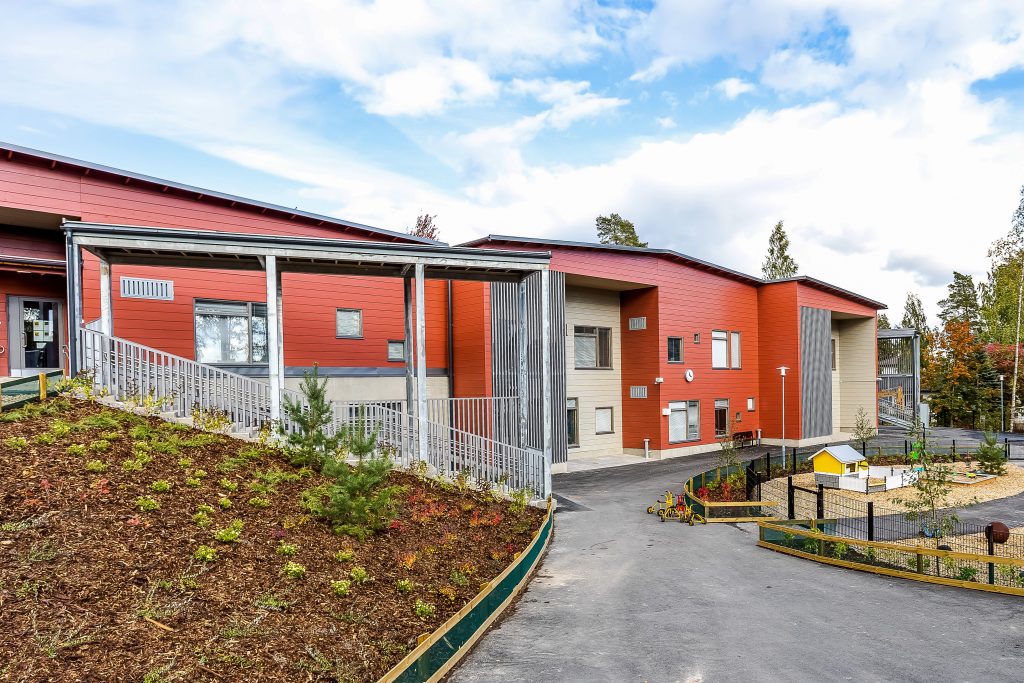
CONTRACTING MODEL | BEST FOR | NOTES |
Fixed-price | Projects built using traditional methods, such as building on site. Projects where contracts for wooden components, such as skeleton framed planar elements for exterior walls, can be tendered and subcontracted among several suppliers. | Clients may be exposed to price risks in a traditional fixed-price call for tenders. If the proposed wooden structure system, its suppliers, subcontractors and cost structure are unfamiliar to the bidding contractors, they may calculate a potential price risk into their bids. If this is the case, the recommendation is to have a separate procurement contract (split contract) for the wooden components. |
Split | Projects where it makes sense for the client to tender a separate procurement contract for the wooden components due to the scope of the procurement, the limited number of suppliers, or some other reason. | If there is reason to believe that wooden construction components will make up too high a share of the costs in a normal bidding process, clients can procure them separately by issuing a call for tenders directly to manufacturers. |
Turnkey | Projects that are interested in receiving competing bids that are based on different structural systems. Projects that aim to have bidders compete on quality within a given cost framework and that want a straightforward construction process. Projects where collaboration between design and construction in the very early stages of the project is considered useful. | There is a wealth of material, frame system, and production method options available in wood construction. If one is chosen early in the design phase, then the number of possible suppliers is significantly limited. Turnkey tendering levels the competitive playing field for the different material, frame system, and production method options. In wooden construction, it is often smart to get construction contractors involved in the planning process. This approach ensures that the overall design is feasible and that someone is available to build it. |
Project management contract | Projects that are technically or functionally challenging and have higher risks and/or development opportunities. | Tender negotiations on contracts, content of plans and quality requirements or development workshops on project development are needed. Requires know-how and resources from the customer during the construction |
Alliance | Projects that seek to promote the evolution of new cost-effective solutions and operating methods. | Requires know-how and resources from the customer in the development and construction phases. A new kind of decision-making is required |
Public-private partnership | Projects that want the contractor to make a strong commitment to a building’s safety in use, for example to prevent indoor air issues, and to ensure that the building is constructed to be cost-efficient in the long run. | Determine the level of condition required of the building at the end of the life cycle contract The length of the life cycle contract should be set taking into account the life cycle of the building’s systems and structures as well as maintenance and renewal needs. |