
Solid wood panel elements with nailed joints
Northern Karelia’s Karelia Puutec has developed a non-glued CLT panel that brings something new to the product range for wooden construction panels.
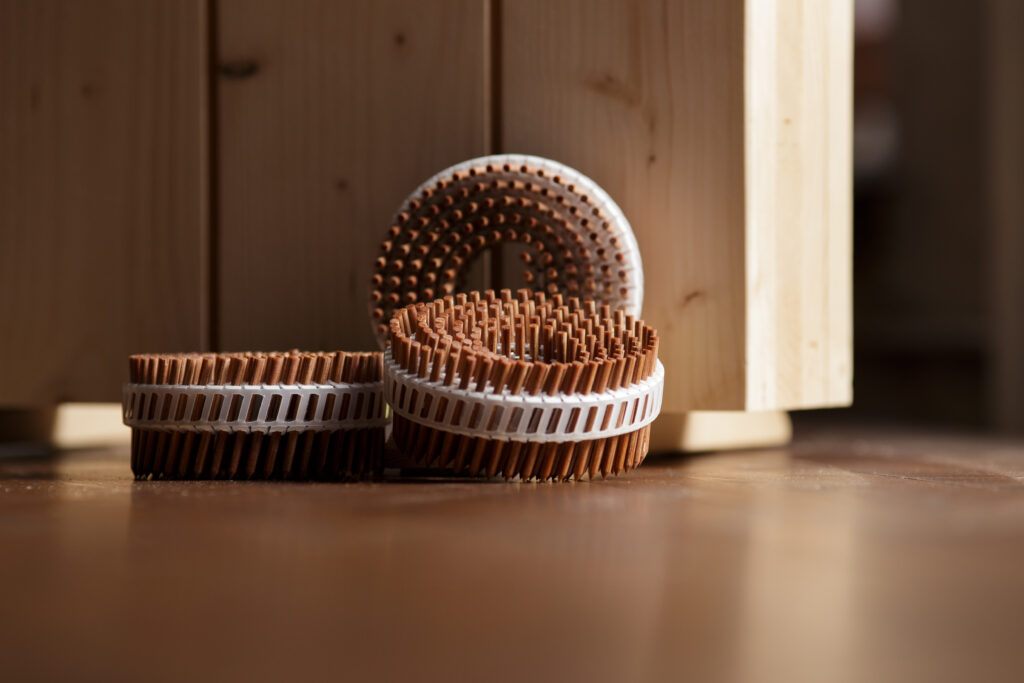
Environmental friendliness has been a core value of the development process, which includes a local supply chain, low production emissions, and a circular economy for materials. By enabling modifiable structures, the product presents numerous architectural opportunities.
Read the article in Finnish here.
Preliminary studies determined there was enough innovative value in the product to warrant a patent application. Although nailed solid wood panels are quite common in central Europe, the panels of Karelia Puutec’s competitors require far more nails. Karelia Puutec’s product development aimed to optimise the required number of nails, which required rethinking the directions of the laminations, including the use of slanted layers.
The resulting solution is perfect for agile, small-scale industrial production and is very competitive with industry-produced CLT on price. Replacing beech nails with metal ones would produce additional savings, but this switch would also make the panels harder to machine or recycle.
Karelia Puutec panels can be easily machined to produce large, ready-to-install elements with surfaces that can serve as interior design elements without any cladding. Thanks to grooves cut into the panel surface, gaps caused by the natural expansion/contraction of neighbouring panels remain undetectable.
To illustrate their potential use for saunas and utility buildings, Puutec built a 15 square metre mini-cottage from these nailed solid wood panels. The mini-cottage also demonstrates other advanced construction techniques, such as combining settling and non-settling structures into a single structure. The log partition wall is connected to the non-settling panel wall using a special Karelia Puutec joint that is a protected design.
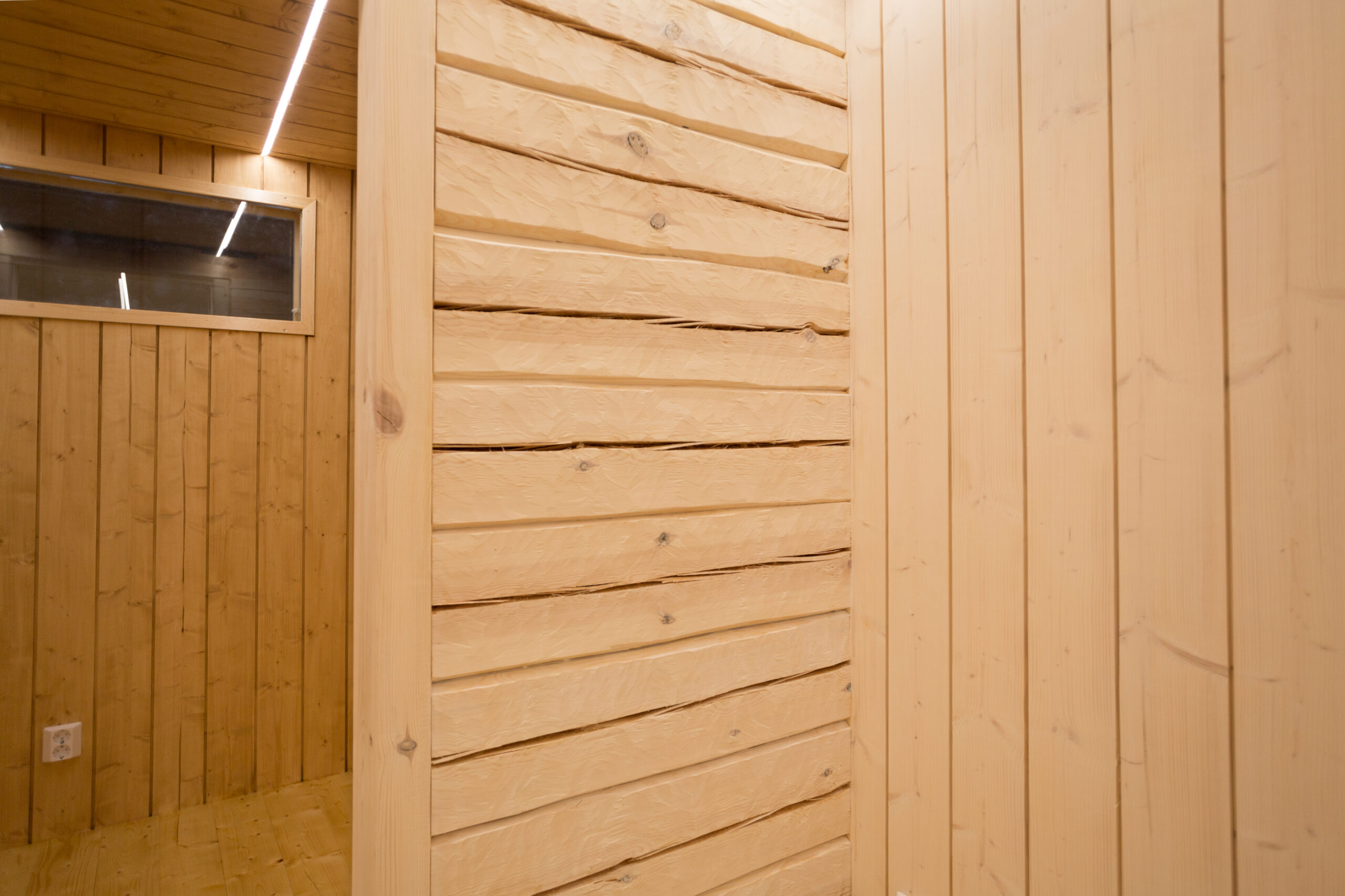
Despite the company’s small scale of production, frameworks can already be installed inside the panels at the production site. Openings in the panels are also cut during the laminating process. This high degree of readiness also enables electrical, window, and door work to be done during the production phase, if desired. Reducing waste by further optimising the use of raw materials is one of the goals of production development. Puutec wants to develop solutions where the wood is processed as little as possible and uses as little energy as possible, with the ultimate goal of producing entire buildings at its facility.
Karelia Puutec only uses local lumber that comes from within a radius of about 50 kilometres. This results in a significant reduction in emissions during the production chain’s product phase and provides employment opportunities in nearby areas. The LÄHIPUU® trademark indicates the products’ value chain has a positive impact on the local area.
CREDITS
Riku Mantsinen, an entrepreneur from Joensuu, began to focus on wood construction more than 20 years ago, when he built a small house. At that time, CLT was already making headlines in Northern Karelia, as were non-glued panels. Mantsinen worked for the last decade in the wooden and renovation construction sector and had the idea of developing his own non-glued panel, the largest drivers being his environmental values and interest in using nearby raw materials. His company wanted to make non-glued panels with raw materials that would qualify them for the Lähipuu trademark to indicate their commitment to using renewable energy and locally-produced materials.